Straw Recycling: Pyrolysis vs. Incineration
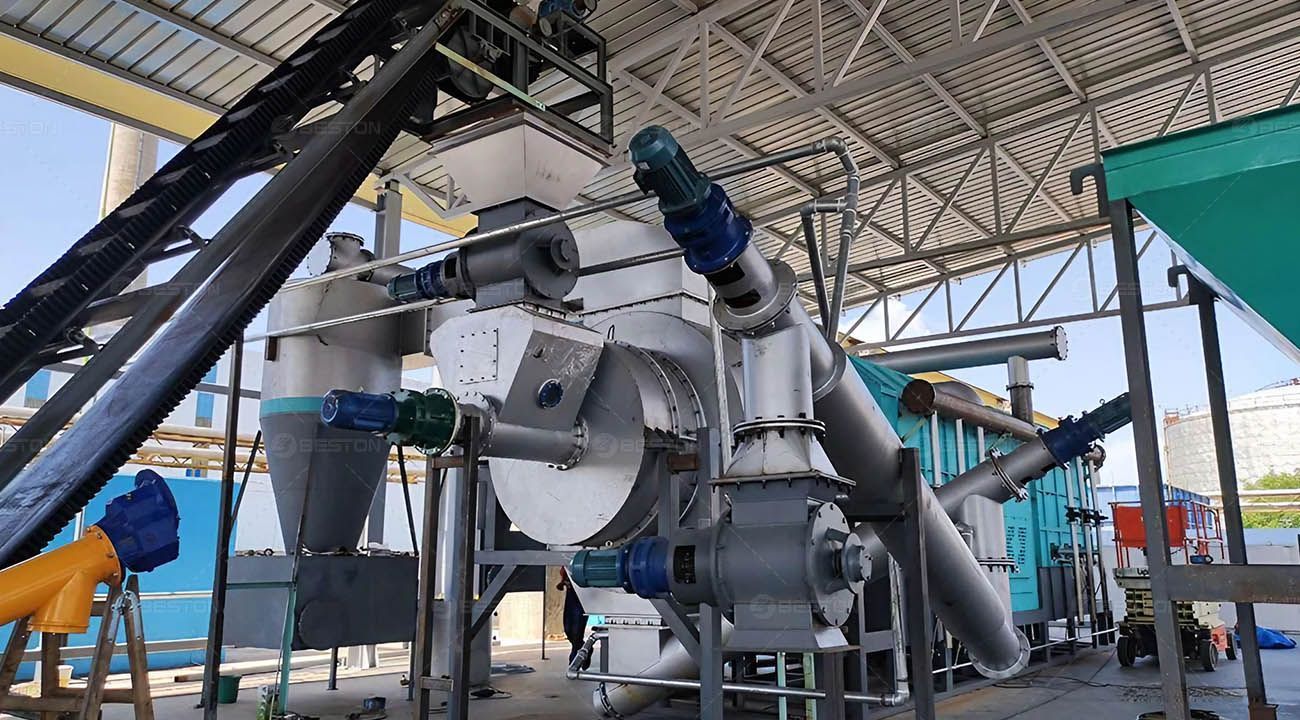
Straw, an abundant agricultural byproduct, has long been considered a waste material. However, with growing concerns over environmental sustainability and waste management, it has become a valuable resource for energy production and soil enhancement. Among the various methods for recycling straw, pyrolysis and incineration are two commonly employed techniques. Both processes offer distinct advantages and limitations when it comes to converting straw into useful products, such as energy, biochar, or other byproducts. Understanding the differences between these two methods is crucial for making informed decisions in waste management and resource recovery.
Pyrolysis: A Sustainable Approach
Pyrolysis is a thermochemical process that decomposes organic materials in the absence of oxygen, typically at temperatures ranging from 300°C to 900°C. During this process, straw undergoes thermal degradation, resulting in the production of biochar, oil, and gas. The key benefit of pyrolysis is its ability to generate valuable byproducts while minimizing harmful emissions.
The straw charcoal machine is specifically designed to facilitate the pyrolysis process. It ensures that straw is heated in a controlled environment, where the absence of oxygen prevents complete combustion. As a result, the organic matter is broken down into carbon-rich biochar, which can be used to improve soil fertility or as a fuel source. The liquid and gaseous byproducts produced during pyrolysis, such as bio-oil and syngas, can be further processed and utilized as renewable energy sources, making the entire process highly efficient and sustainable.
One of the primary advantages of pyrolysis over incineration is its ability to sequester carbon in the form of biochar. Biochar is a stable, carbon-rich material that can be stored in soil for long periods, effectively removing carbon from the atmosphere and helping mitigate climate change. Furthermore, the gaseous byproducts, which include methane, carbon monoxide, and hydrogen, can be captured and used for energy production, further enhancing the environmental benefits of the process.
Incineration: A Simpler, High-Temperature Process
Incineration, on the other hand, is a high-temperature combustion process that involves burning straw in the presence of oxygen. The primary objective of incineration is to reduce the volume of waste by converting it into ash, heat, and gases. While incineration is a well-established method for waste disposal, it presents several environmental challenges compared to pyrolysis.
When straw is incinerated, the combustion process generates significant amounts of carbon dioxide (CO2), a greenhouse gas that contributes to global warming. Additionally, incineration can produce other harmful pollutants, such as particulate matter, nitrogen oxides (NOx), and sulfur dioxide (SO2), which can negatively impact air quality and human health. Although modern incinerators are equipped with pollution control systems to mitigate these emissions, the overall environmental impact of incineration is still higher than that of pyrolysis.
Another drawback of incineration is the lack of valuable byproducts. While pyrolysis produces biochar, oil, and gas, incineration primarily generates ash, which is often discarded or landfilled. In some cases, the ash can be used as a fertilizer or in construction materials, but these applications are limited compared to the versatile uses of biochar and other pyrolysis byproducts.
Environmental Impact: Pyrolysis vs. Incineration
The environmental impact of both pyrolysis and incineration largely depends on the specific conditions under which the processes are carried out. However, pyrolysis generally offers a more sustainable solution for straw recycling due to its ability to reduce harmful emissions, produce valuable byproducts, and sequester carbon in the form of biochar.
In contrast, incineration, while effective for waste disposal, tends to release more CO2 and other pollutants into the atmosphere. The lack of useful byproducts from incineration also limits its overall environmental benefits. Pyrolysis, on the other hand, contributes to waste-to-energy conversion while simultaneously addressing carbon sequestration and soil enhancement.
Economic Considerations
From an economic perspective, both pyrolysis and incineration require significant capital investment in equipment and infrastructure. A straw charcoal machine, for example, can be a costly investment for pyrolysis-based operations, though the potential for producing biochar and renewable energy can offer long-term financial returns. The ability to sell byproducts such as bio-oil and syngas can help offset operational costs and increase profitability.
Incineration, while generally less expensive in terms of equipment and maintenance, may face higher costs related to air pollution control and waste disposal. Additionally, the lack of valuable byproducts from incineration means that the economic returns are more limited compared to pyrolysis.
Choosing the Right Method for Straw Recycling
When deciding between pyrolysis and incineration for straw recycling, several factors must be considered, including environmental impact, economic feasibility, and the desired end products. Pyrolysis offers a more sustainable solution with the potential for valuable byproducts and carbon sequestration, making it a preferable choice for long-term waste management and resource recovery. However, incineration remains a viable option for regions where waste disposal is the primary concern and environmental regulations are less stringent.
Ultimately, the choice between pyrolysis and incineration depends on the specific goals and circumstances of the recycling operation. Both methods have their place in straw recycling, but for those seeking a more environmentally friendly and economically viable solution, pyrolysis stands out as the more sustainable option.
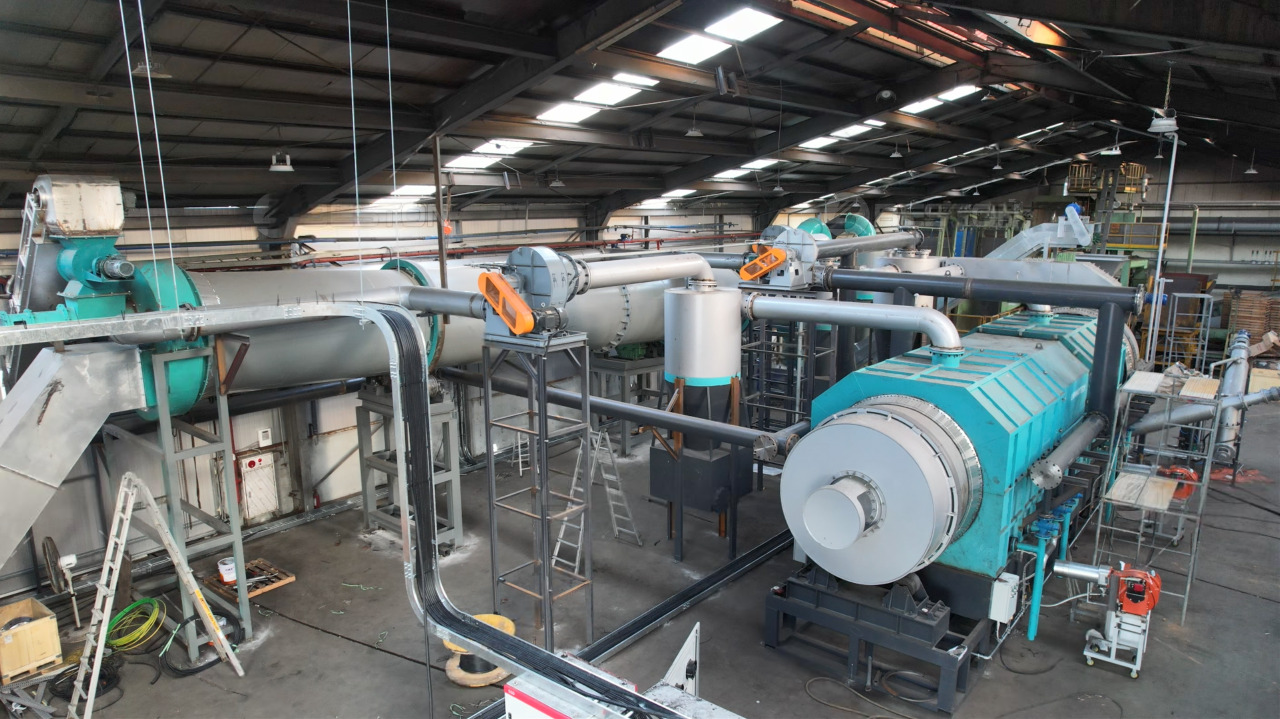
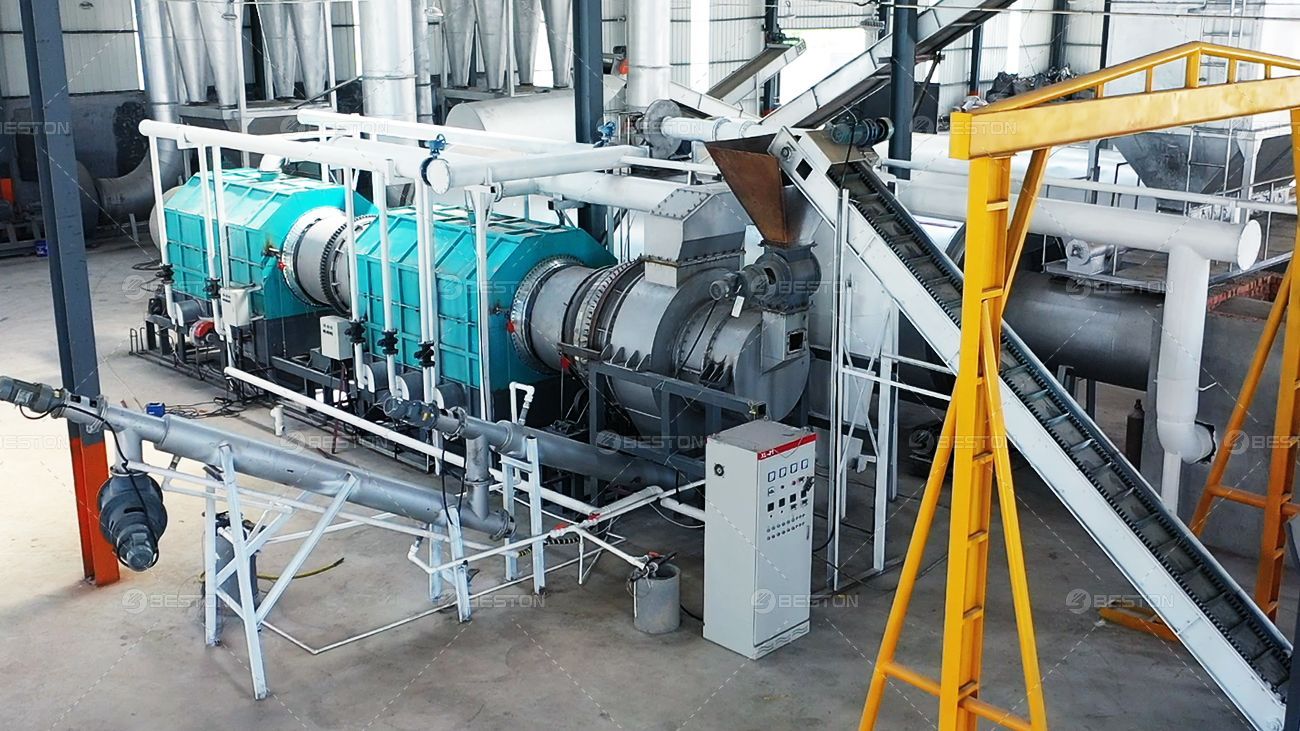
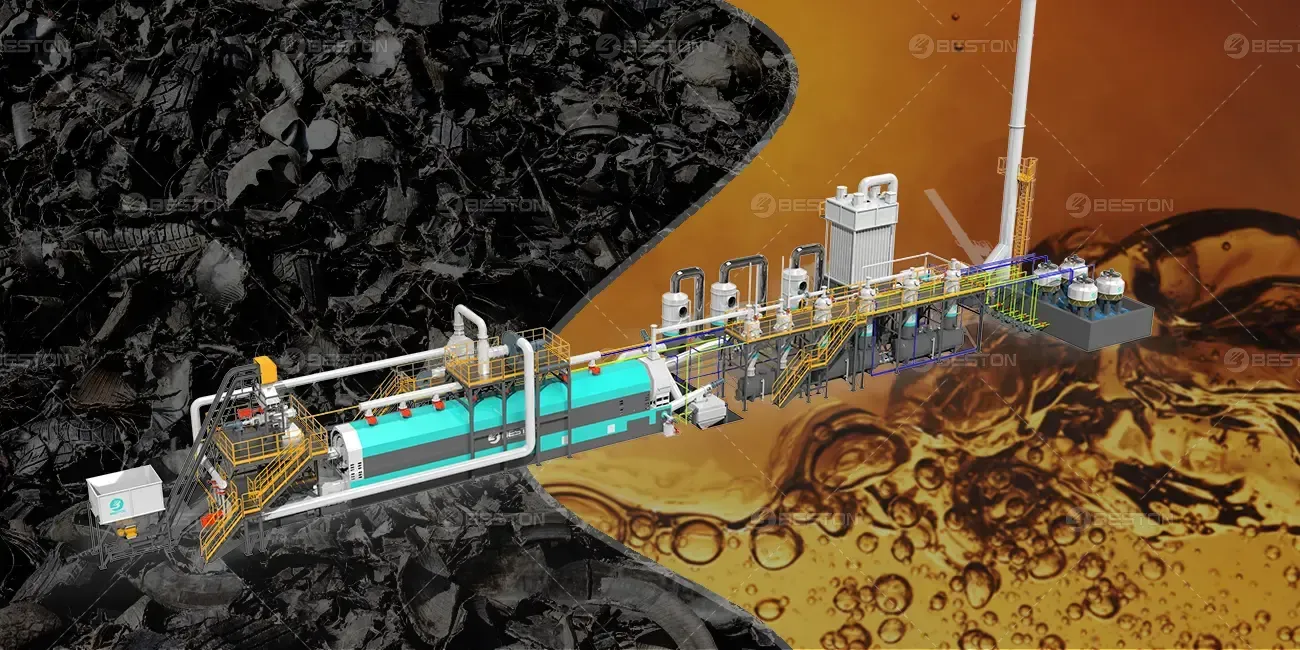