Palm Waste for Biochar Production: A Sustainable Solution
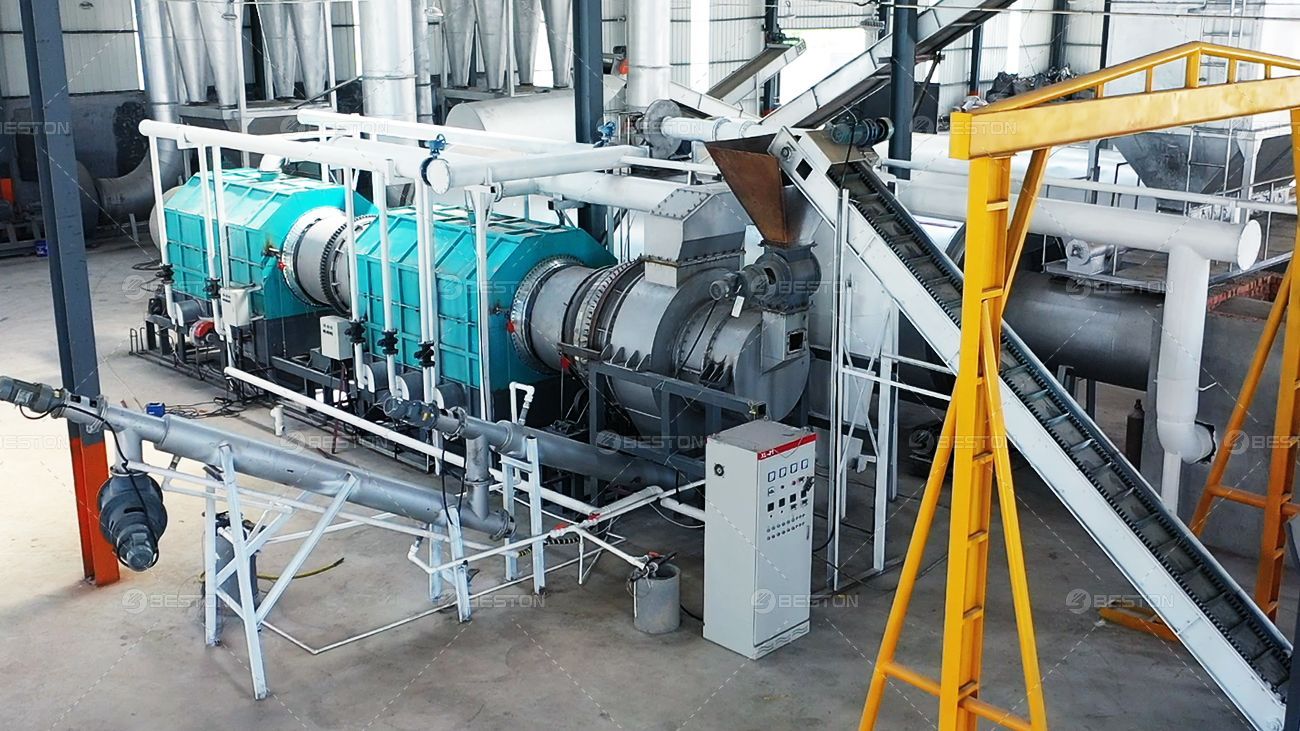
The increasing demand for renewable energy and sustainable agricultural practices has brought attention to biochar as a valuable resource. Biochar, a carbon-rich material produced through pyrolysis, offers a range of environmental benefits. While a variety of feedstocks can be used to produce biochar, palm waste, specifically palm kernel shells, empty fruit bunches, and palm fronds, presents a highly efficient and sustainable option. Using a biochar machine to process palm waste not only addresses the waste management challenge in palm oil production but also offers multiple environmental and economic advantages.
Efficient Waste Management in Palm Oil Production
Palm oil production, a significant industry in tropical countries like Indonesia and Malaysia, generates large volumes of waste. This includes materials such as empty fruit bunches, palm kernel shells, and fronds, which are often discarded or burned, contributing to environmental pollution. By using a biochar machine to convert palm waste into biochar, these by-products can be transformed into a valuable resource, reducing waste and minimizing environmental harm.
Biochar production from palm waste provides a practical solution for managing agricultural residues. Instead of being incinerated or left to decompose, which can produce harmful greenhouse gases, the palm waste is thermochemically processed at high temperatures in the biochar machine, creating a stable form of carbon that can be stored in the soil for long periods. This reduces carbon emissions and the risk of soil degradation associated with open-air burning or improper disposal methods.
Enhancing Soil Fertility and Agricultural Productivity
One of the most significant benefits of biochar produced from palm waste is its ability to improve soil fertility. When applied to agricultural soils, biochar acts as a soil conditioner, enhancing its physical and chemical properties. The porous structure of biochar increases the soil’s water-holding capacity, improves aeration, and facilitates better root growth. It also helps retain nutrients, reducing the need for synthetic fertilizers and lowering overall agricultural input costs.
Furthermore, biochar has the ability to adsorb harmful substances, such as heavy metals and toxins, which can otherwise contaminate the soil and water. This makes it an excellent tool for remediation of degraded soils, particularly in areas affected by industrial pollution or overuse of chemical fertilizers.
Carbon Sequestration and Mitigating Climate Change
The process of producing biochar from palm waste offers significant potential for carbon sequestration. During pyrolysis, carbon from the palm waste is captured and stored in a stable form as biochar, preventing it from being released as carbon dioxide or methane into the atmosphere. This process locks away carbon for long periods—potentially hundreds or even thousands of years—thereby contributing to climate change mitigation.
Biochar’s ability to sequester carbon makes it an effective tool in global efforts to reduce atmospheric greenhouse gases. By diverting palm waste from incineration or landfilling and converting it into biochar, large amounts of carbon can be stored, reducing the overall carbon footprint of palm oil production. In this way, palm waste management can become part of a broader strategy for addressing climate change.
Renewable Energy Production and Cost Efficiency
In addition to producing biochar, the pyrolysis process in the palm shell charcoal machine generates bio-oil and syngas, both of which can be used as renewable energy sources. Bio-oil, a liquid by-product of the process, can be refined into a substitute for petroleum-based fuels or used directly to power the biochar machine itself. Syngas, a mixture of hydrogen, carbon monoxide, and other gases, can be burned to generate heat and electricity, reducing the need for external energy sources.
This closed-loop system not only makes the biochar production process more energy-efficient but also creates a source of renewable energy. The ability to produce bio-oil and syngas from palm waste adds an economic benefit to the biochar production process, offsetting operational costs and making the process more financially viable.
Environmental and Economic Benefits
Utilizing a biochar machine to produce biochar from palm waste has far-reaching environmental and economic benefits. The primary environmental advantage is waste reduction. By converting palm waste into biochar, harmful emissions from burning and landfilling are minimized, contributing to cleaner air and water quality. Moreover, biochar’s role in carbon sequestration helps mitigate the impacts of climate change.
Economically, biochar production can open new revenue streams for palm oil producers and agricultural stakeholders. In regions with abundant palm waste, the biochar machine offers an opportunity to turn waste into a valuable product. Biochar can be sold as a soil amendment, used in carbon credits programs, or even processed into activated carbon for industrial uses. Additionally, the energy by-products of the pyrolysis process can reduce the need for external energy inputs, cutting operational costs and increasing profitability.
The implementation of biochar technology also aligns with growing consumer and regulatory demands for sustainability. With increasing awareness of environmental issues, companies that incorporate sustainable waste management practices and carbon sequestration strategies gain a competitive edge in the market.
Scalable and Versatile Technology
The use of a biochar machine to process palm waste is a highly scalable and versatile solution. Small-scale operations can be established for local use, while larger facilities can handle substantial amounts of palm waste, making it suitable for diverse operational scales. The technology is adaptable and can process a wide range of feedstocks beyond palm waste, such as wood chips, agricultural residues, and other biomass materials. This makes biochar production an attractive option for regions involved in various forms of biomass production.
Additionally, biochar technology is evolving with continuous improvements in machine design and process efficiency. New advancements are increasing the throughput, reducing energy consumption, and enhancing the quality of the biochar produced. As demand for biochar increases, further innovations will make the process more efficient and accessible to a broader range of industries.
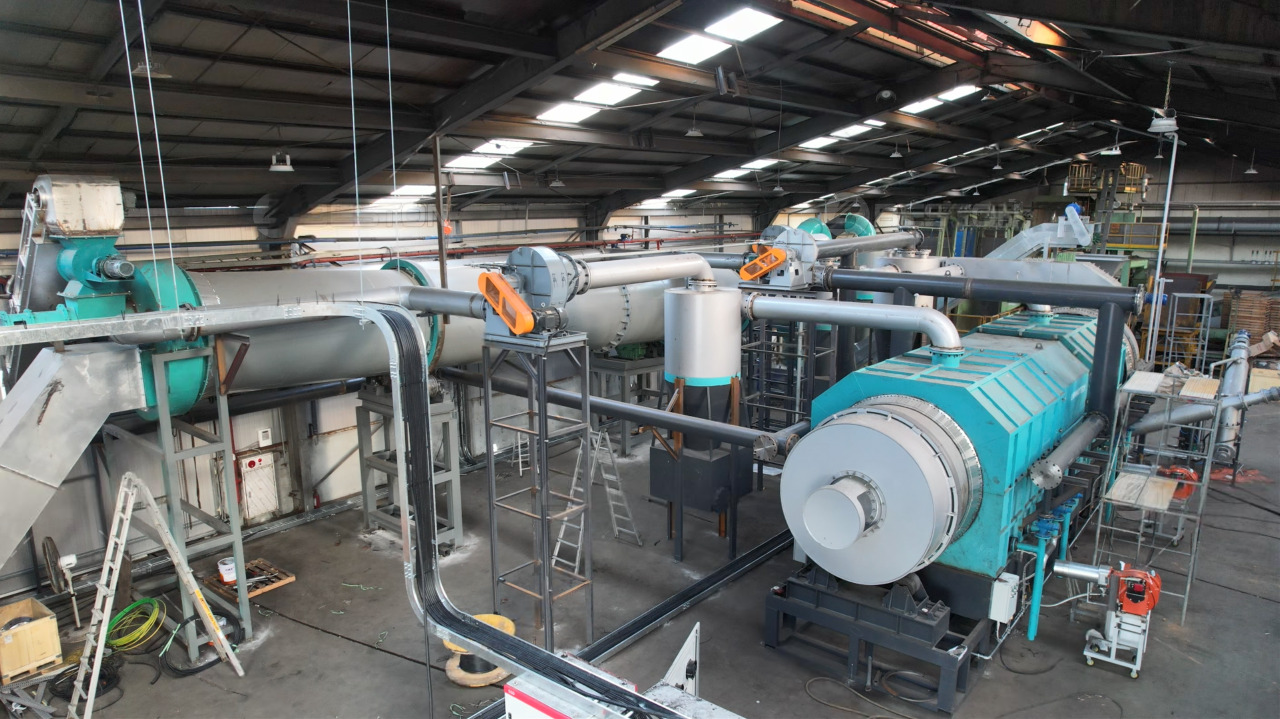
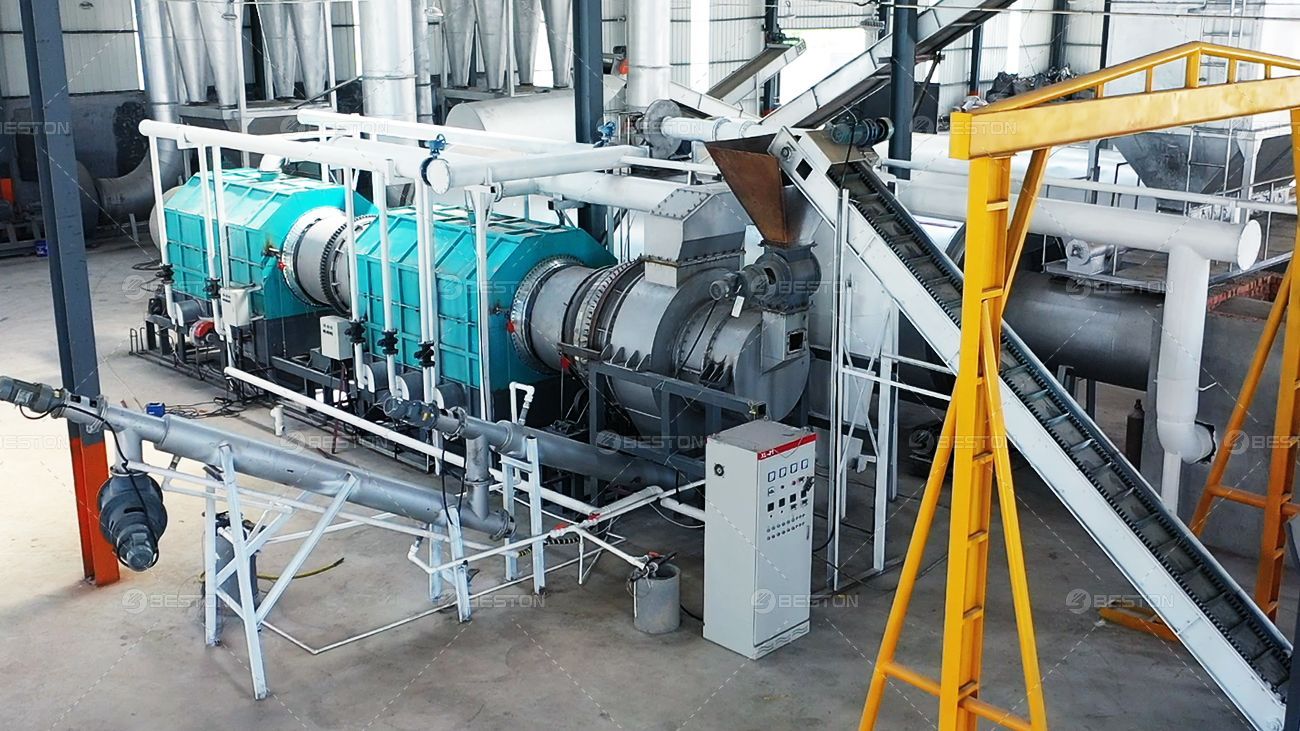
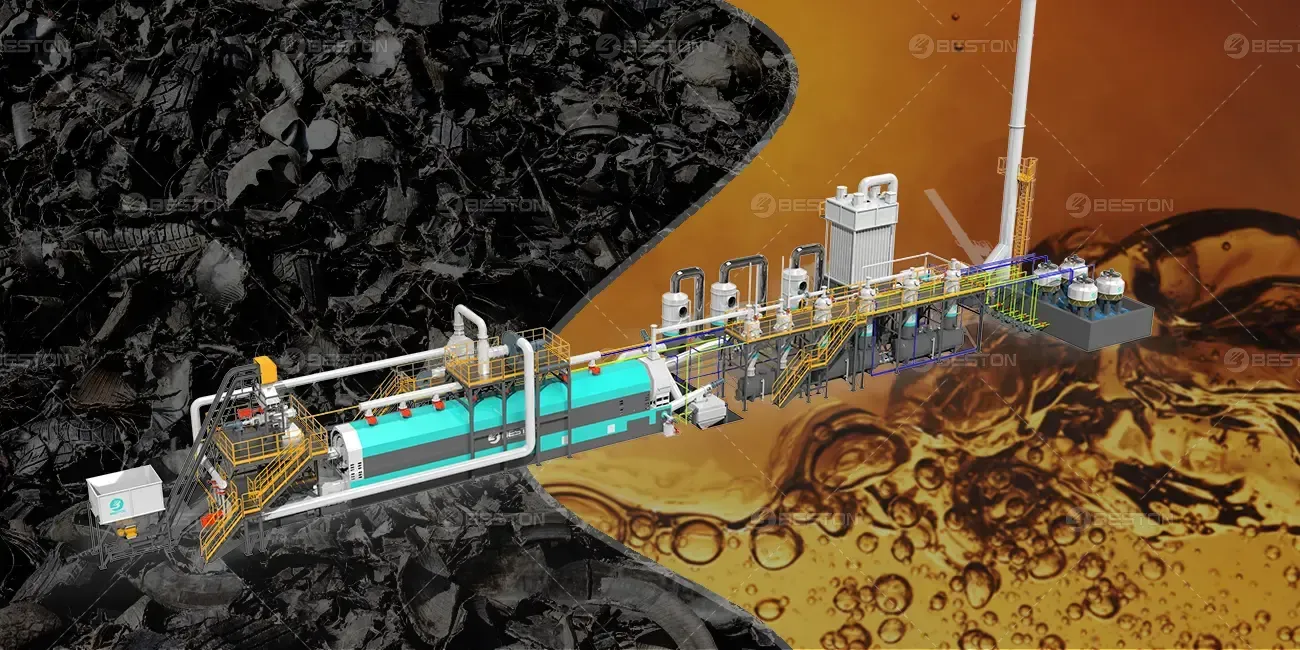