How to Maintain a Pyrolysis Reactor for Optimal Performance
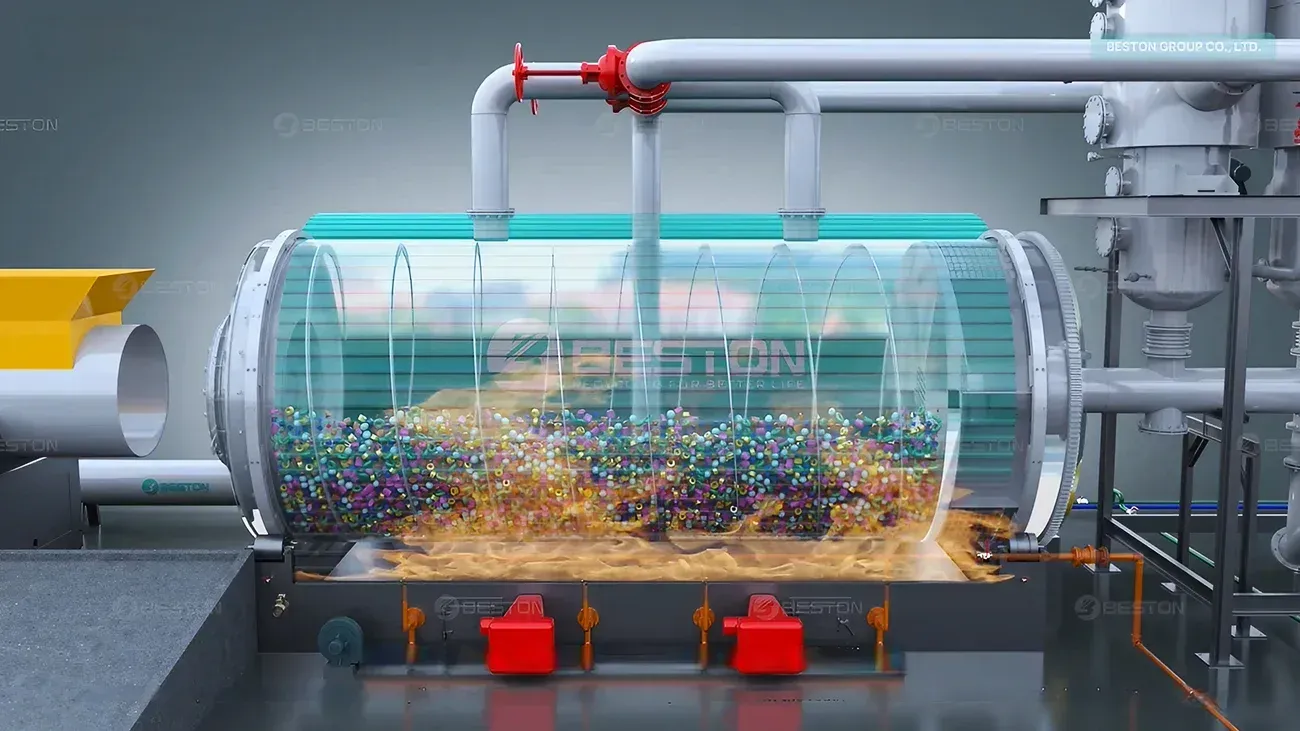
Pyrolysis reactors are integral to the thermal decomposition of organic materials, providing an environmentally-friendly approach to recycling waste into useful byproducts such as biochar, fuel oil, and syngas. However, maintaining a pyrolysis reactor requires meticulous attention to detail and a proactive approach to ensure safe and efficient operation. This guide delves into the essential practices for maintaining a pyrolysis reactor, enhancing its lifespan and ensuring consistent performance.
1. Regular Inspection of Reactor Components
Consistent inspection is fundamental to the maintenance of a pyrolysis reactor. Over time, high temperatures and reactive materials can cause wear and degradation. Key areas to inspect include:
- Reactor Vessel: Examine for signs of cracking, corrosion, or material degradation. Pay particular attention to areas near heating elements and points of contact with high-heat materials.
- Seals and Gaskets: Regularly assess seals and gaskets for wear or leaks. These components ensure the airtight environment crucial for pyrolysis and prevent hazardous gas emissions.
- Piping and Valves: Check for any obstructions, leaks, or irregularities in valves and pipelines. Blockages can compromise pressure levels and impede the flow of byproducts.
- Heating Elements: Evaluate the condition of the heating system, ensuring that elements distribute heat evenly and achieve target temperatures efficiently.
Routine inspections should be conducted with appropriate safety equipment, as some areas may retain residual heat or reactive substances. Scheduled visual inspections help identify early signs of wear and preempt issues that could escalate into operational failures.
2. Monitoring Temperature and Pressure Controls
Temperature and pressure are critical to achieving the precise conditions required for pyrolysis. Maintaining these parameters within optimal ranges prevents unexpected reactions and maximizes reactor efficiency.
- Temperature Sensors: Check the calibration of sensors regularly. Accurate readings are essential for the process, and any deviation in calibration could lead to energy inefficiency or potential safety hazards.
- Pressure Gauges: Monitor pressure gauges to ensure stable internal conditions. Pressure fluctuations can indicate blockages or seal degradation, necessitating immediate attention.
- Automated Control Systems: Many reactors use PLC (Programmable Logic Controller) systems to manage these variables. Ensure that these systems receive regular software updates and functional checks to maintain their reliability.
Consistent calibration and monitoring not only extend the lifespan of reactor components but also safeguard against abrupt temperature spikes or pressure drops, which can damage the reactor.
3. Cleaning and Decontamination
Reactors for waste pyrolysis plant accumulate residues over time, which can interfere with the process and degrade product quality. Implement a rigorous cleaning schedule to keep the reactor’s internal environment free from obstructions and contaminants.
- Char and Ash Removal: Char and ash deposits can hinder heat distribution and reduce the reactor's efficiency. Cleaning out these residues after each batch helps maintain optimal thermal conductivity.
- Reactor Wall Scraping: High-temperature reactors often experience carbon buildup on the walls. Manual or automated scraping can prevent these deposits from becoming problematic. Choose cleaning methods that won’t scratch or degrade the reactor walls.
- Condensers and Gas Lines: Regularly clear condensers and gas lines to prevent clogging from oil residues or tar, which can compromise gas flow and pressure regulation.
Using a non-abrasive, high-temperature cleaning agent for decontamination is recommended. This prevents the introduction of foreign substances while ensuring the reactor remains functional and efficient.
4. Lubrication and Mechanical Maintenance
Pyrolysis reactors have multiple moving parts, including feed mechanisms, discharge systems, and valves, which require regular lubrication to function seamlessly. Proper lubrication reduces friction, minimizes wear, and prevents overheating in critical components.
- Feed Mechanism: A smooth feed mechanism ensures a steady flow of material, which is essential for uniform pyrolysis. Lubricate gears and moving parts to avoid jamming and irregular feeding.
- Discharge System: The discharge system, particularly in continuous reactors, handles high temperatures and frequent material outflow. Regular lubrication of these parts prevents overheating and extends service life.
- Valves and Actuators: Valves and actuators, which regulate the flow of gases and feedstock, require periodic lubrication and inspection for wear. Replace any components showing signs of damage to avoid operational delays.
Use high-temperature lubricants specifically designed for industrial applications. Low-quality or incompatible lubricants can deteriorate quickly under high temperatures, leaving residue that hampers movement.
5. Ensuring Proper Safety Systems and Emergency Protocols
Safety is paramount when operating a pyrolysis reactor, as the high temperatures and flammable byproducts can create hazardous conditions. Equip the reactor with comprehensive safety features and review emergency protocols regularly.
- Gas Detection Systems: Install gas sensors to monitor potential leaks. Carbon monoxide and other volatile gases can be hazardous, so early detection systems are essential for operator safety.
- Emergency Shutoff Valves: Ensure emergency shutoff valves are in place and functional. These systems automatically halt operations in case of irregular pressure or temperature changes.
- Explosion-Proof Components: Many reactors incorporate explosion-proof designs. Verify that these components are intact, as pressure irregularities or system malfunctions can otherwise lead to dangerous outcomes.
Training staff on emergency procedures and performing regular safety drills ensures a rapid response to potential hazards. Prioritize safety checks and ensure all workers are familiar with reactor emergency protocols.
6. Maintaining a Log of Maintenance Activities
A detailed maintenance log is essential for tracking the health and performance of a pyrolysis reactor. Documenting each maintenance task, along with inspection results and component replacements, offers valuable insight into recurring issues and component lifespan.
- Routine Inspections and Results: Record the results of every inspection, noting any observations, irregularities, or repairs conducted.
- Repairs and Replacements: Log each part replacement, including installation dates, supplier details, and warranty information.
- Operational Metrics: Keep track of temperature, pressure, and output performance metrics over time. This data helps identify any declines in efficiency or emerging patterns that may signal wear.
Regular review of the maintenance log allows operators to identify potential improvements, optimize reactor performance, and forecast the need for replacements before issues become critical.
Conclusion
A well-maintained pyrolysis reactor not only ensures operational efficiency but also enhances safety and prolongs the lifespan of the machinery. Through regular inspections, precise control of temperature and pressure, thorough cleaning, and consistent mechanical upkeep, operators can mitigate common issues and keep the reactor running at optimal levels. By committing to these best practices, facilities can maximize both output and quality, making the pyrolysis process safer, more reliable, and economically sustainable over the long term.
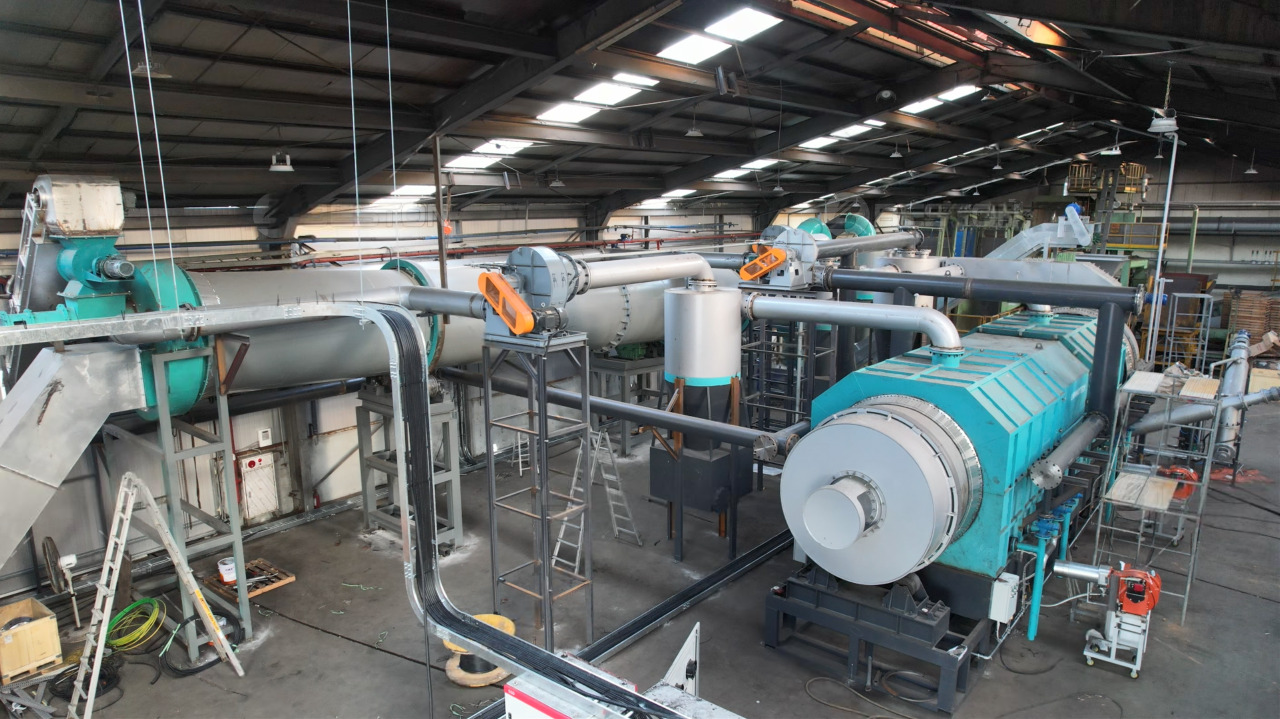
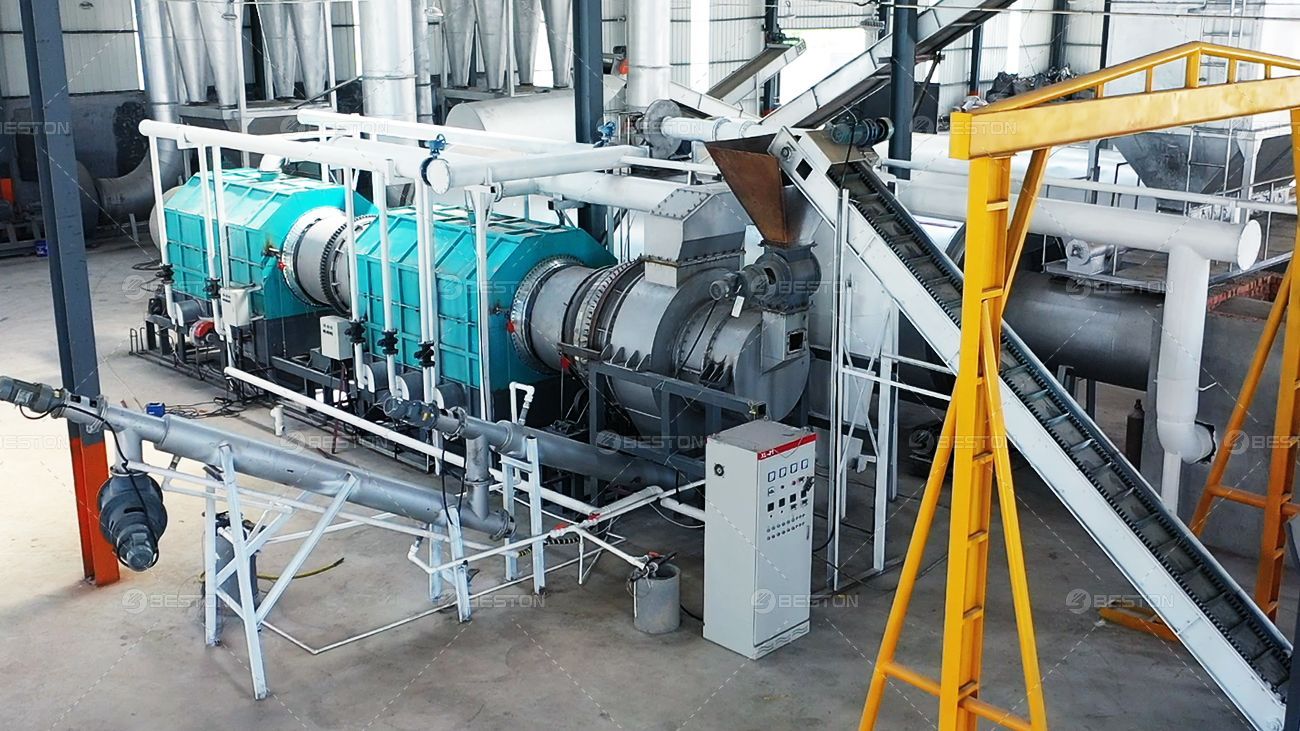
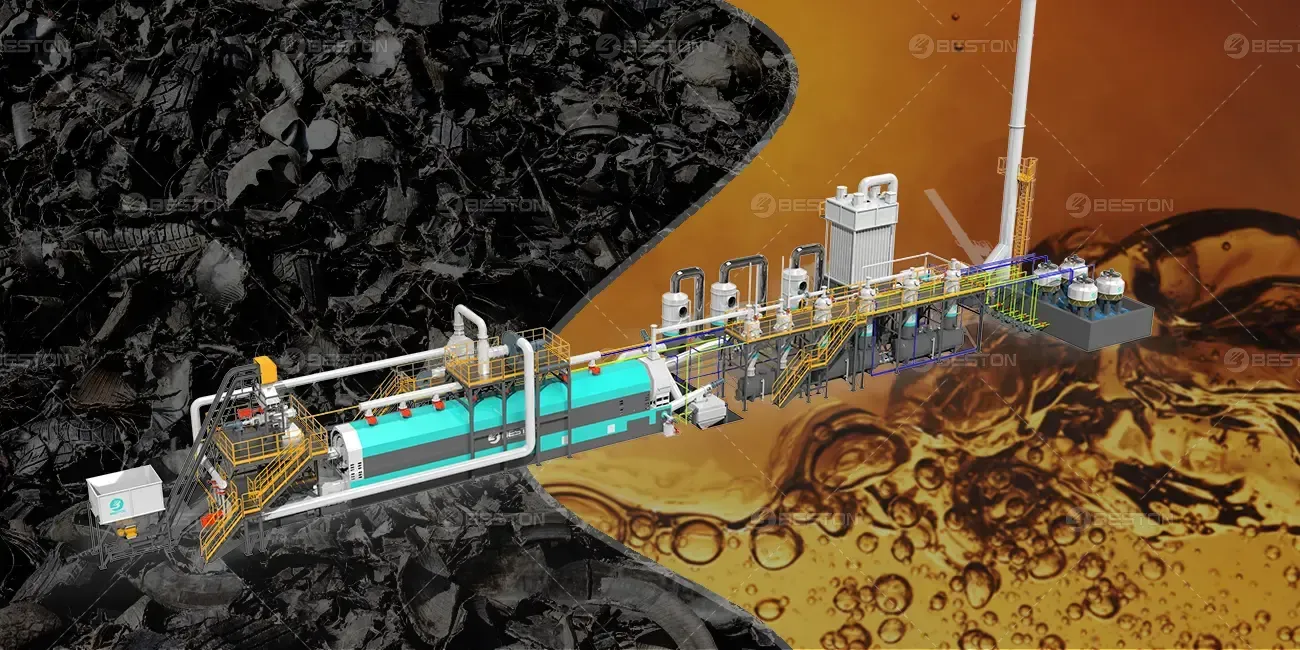