Enhancing the Efficiency of Plastic-to-Oil Conversion
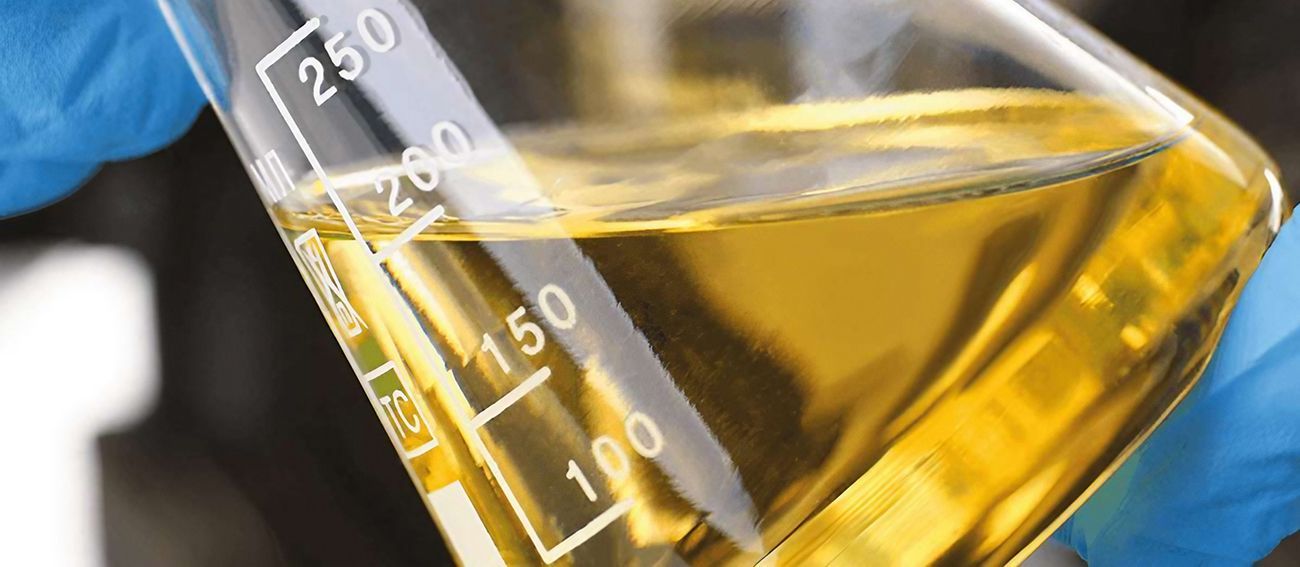
Plastic waste represents both an environmental challenge and an untapped energy resource. Converting plastic into fuel through pyrolysis offers a viable solution to plastic pollution while generating valuable hydrocarbon products. However, to maximize the economic and environmental benefits, it is crucial to optimize the efficiency of the plastic-to-oil process. Various factors, including feedstock preparation, reactor design, and process conditions, significantly impact the yield and quality of the final product.
Optimizing Feedstock Selection and Preparation
The composition and pre-treatment of plastic feedstock play a fundamental role in the efficiency of the pyrolysis process. Not all plastics yield the same volume or quality of oil.
- Sorting and Segregation – Different plastic types exhibit varying thermal degradation behaviors. Polyethylene (PE) and polypropylene (PP) produce high-quality fuel, while polyvinyl chloride (PVC) releases harmful chlorine compounds. Efficient sorting mechanisms should be implemented to eliminate non-convertible or problematic materials.
- Pre-treatment and Size Reduction – Shredding plastic into uniform, small particles enhances heat transfer and accelerates pyrolysis. Proper drying is also necessary, as moisture can cause energy losses and affect reaction kinetics.
- Blending for Stability – Combining different plastic types in controlled proportions can optimize the pyrolysis reaction, ensuring a steady thermal breakdown and improving yield consistency.
Improving Reactor Design and Heat Distribution
The efficiency of a plastic to oil machine is largely dependent on the reactor’s ability to maintain uniform thermal conditions and facilitate complete plastic decomposition.
- Continuous vs. Batch Reactors – Continuous pyrolysis systems offer superior efficiency compared to batch reactors. They enable a steady input of feedstock, reduce downtime, and improve overall throughput.
- Heat Transfer Optimization – Uniform heating prevents localized overheating or under-processing. Indirect heating mechanisms, combined with high thermal conductivity reactor materials, enhance energy efficiency and reaction stability.
- Catalyst Utilization – The addition of catalysts, such as zeolites or alumina-based compounds, lowers the pyrolysis temperature and accelerates the breakdown of long-chain polymers. This results in higher-quality fuel, reduced residue formation, and increased overall efficiency.
Process Parameter Optimization
Controlling reaction parameters ensures that the plastic into fuel machine operates at peak efficiency, maximizing fuel yield and minimizing waste by-products.
- Temperature Control – Maintaining an optimal temperature range (typically between 400°C and 500°C) ensures efficient thermal cracking of plastics while avoiding excessive gasification. Deviations can lead to incomplete conversion or unnecessary energy consumption.
- Residence Time Adjustment – The duration that plastic remains in the reactor directly influences yield. A carefully controlled residence time allows complete polymer breakdown without secondary degradation of valuable hydrocarbons.
- Vacuum and Pressure Regulation – Low-pressure pyrolysis can improve fuel recovery by preventing unwanted side reactions. Optimized pressure control systems reduce the formation of non-condensable gases and enhance liquid oil yield.
Enhancing Energy Recovery and By-Product Utilization
A well-integrated pyrolysis system not only improves efficiency but also maximizes the utilization of by-products, reducing overall operational costs.
- Syngas Utilization – Non-condensable gases generated during pyrolysis contain a high calorific value. Instead of flaring, these gases can be used as an energy source to heat the reactor, reducing external fuel requirements.
- Waste Heat Recovery – Implementing heat exchangers and secondary combustion chambers can capture and reuse thermal energy, increasing overall system efficiency.
- Carbon Black Optimization – The solid residue (carbon black) can be refined and repurposed for industrial applications, creating an additional revenue stream and minimizing waste disposal costs.
Advanced Automation and Process Monitoring
Modern plastic to oil machine designs incorporate automation technologies to enhance process control and efficiency.
- Automated Feeding Systems – Ensuring a steady and regulated input of feedstock prevents fluctuations in reactor conditions and maintains consistent output.
- Real-Time Monitoring – Sensors and AI-driven analytics can track temperature, pressure, and gas composition, allowing for dynamic adjustments that optimize yield.
- Predictive Maintenance – Using machine learning algorithms to analyze operational data helps identify potential system failures before they occur, minimizing downtime and extending equipment lifespan.
Strategic Economic and Environmental Considerations
Optimizing the efficiency of plastic pyrolysis extends beyond technical improvements. Economic feasibility and sustainability should also be prioritized.
- Sourcing Low-Cost Feedstock – Establishing partnerships with municipal waste management firms and recycling centers can provide a steady supply of plastic waste at minimal cost.
- Regulatory Compliance and Certification – Meeting environmental standards enhances credibility and opens doors to government incentives or carbon credit trading opportunities.
- End-Product Refinement – Further upgrading pyrolysis oil into diesel or gasoline fractions increases its market value and expands potential buyers.
By integrating these optimization strategies, a plastic to oil machine can operate with higher efficiency, yielding greater economic returns while contributing to global sustainability efforts.
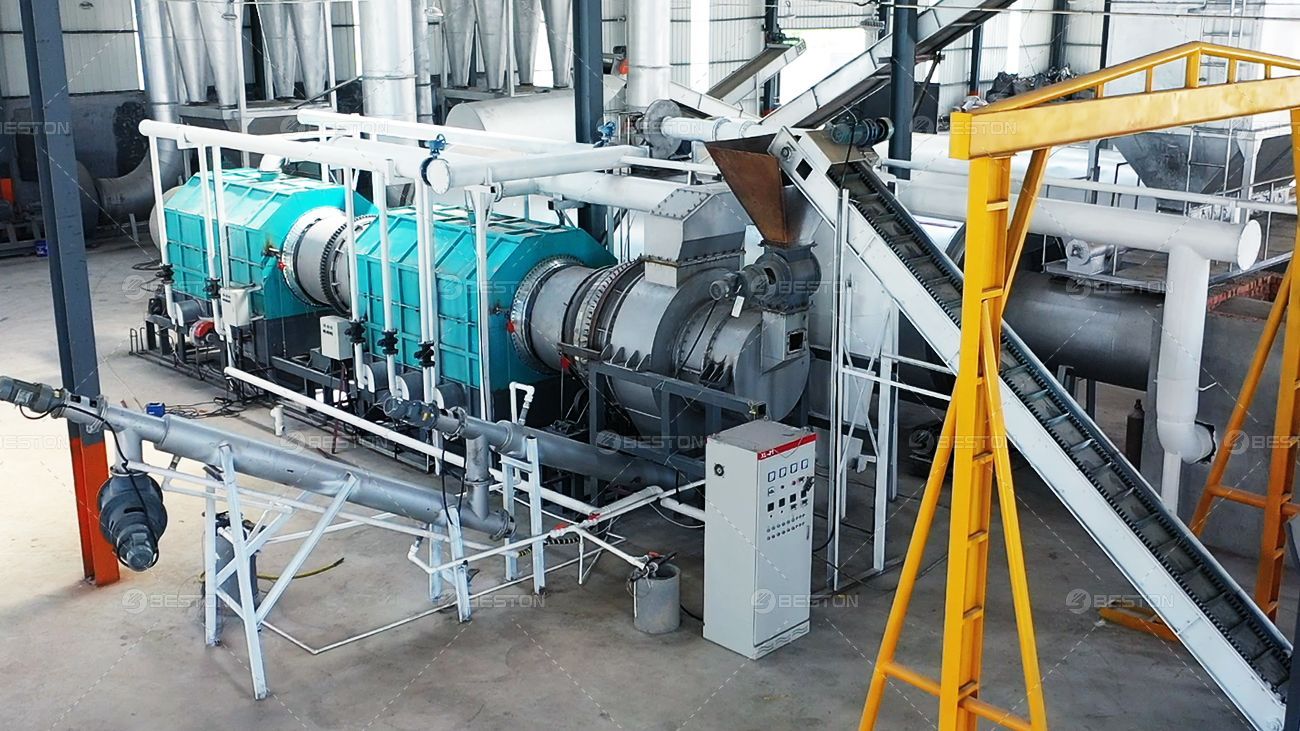
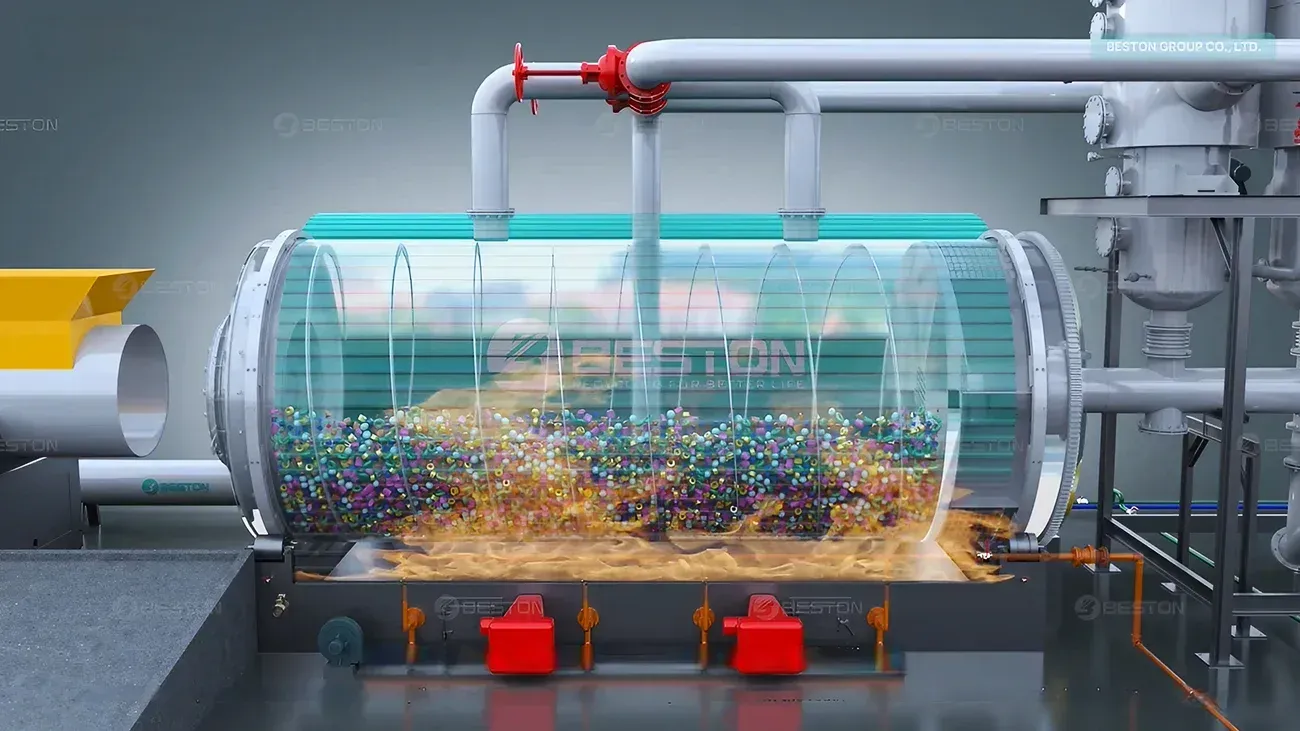
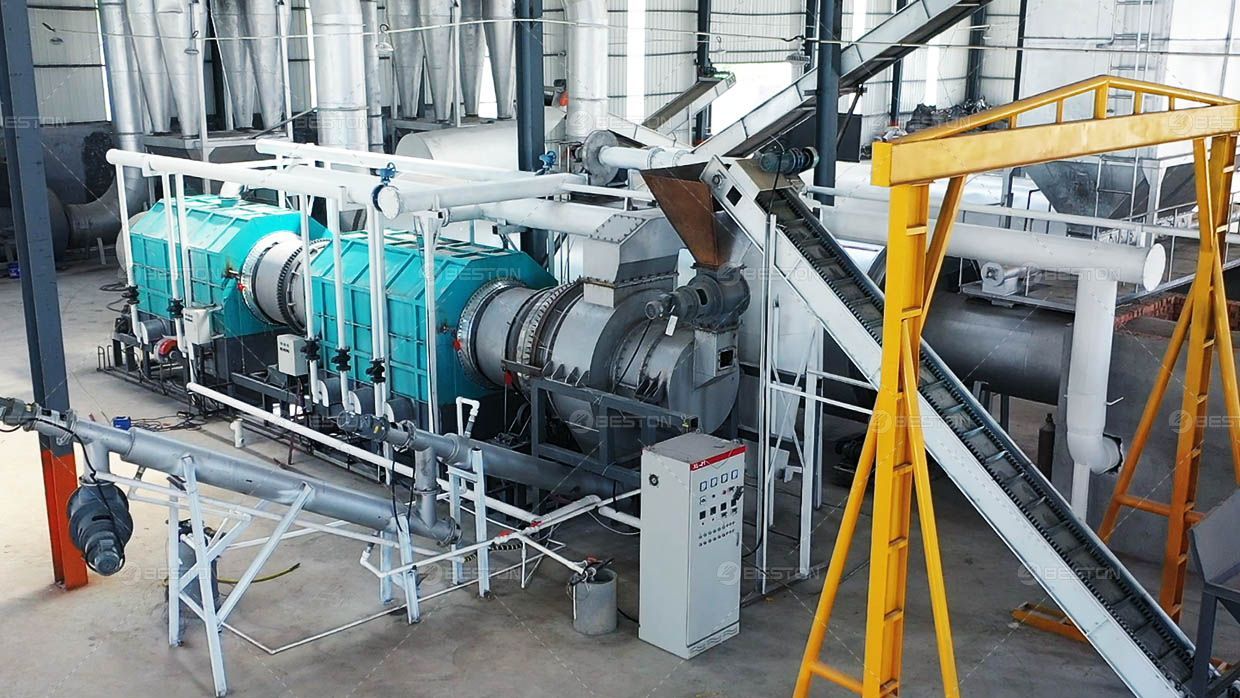