Efficient Oil Sludge Recycling Using Thermal Desorption
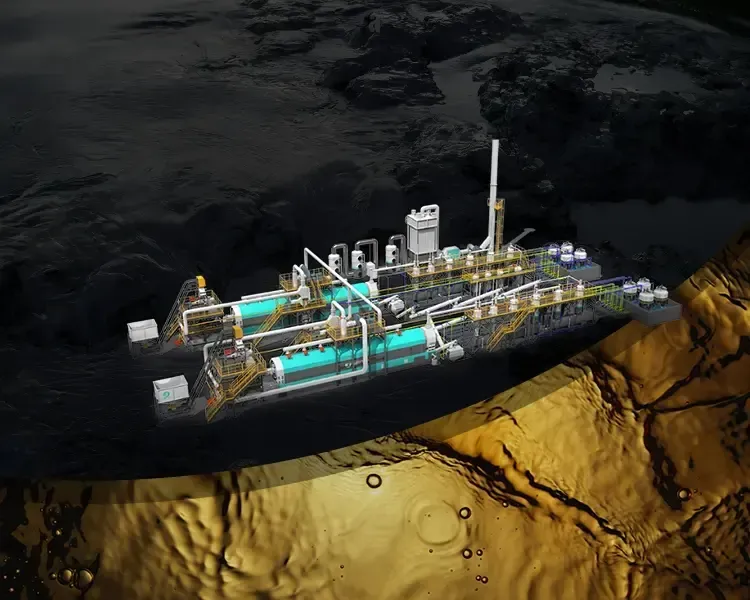
The accumulation of oil sludge is a growing environmental concern due to its hazardous nature and potential to cause severe pollution. Oil sludge, typically generated from industrial processes, can consist of a mixture of oils, water, and solid particulate matter. Improper disposal or storage of this sludge leads to soil and water contamination, making its treatment a priority for industries such as petroleum, chemical processing, and waste management. One promising method for recycling oil sludge in a sustainable manner is thermal desorption. This technique offers an environmentally responsible approach to oil sludge treatment by recovering valuable oil while reducing hazardous waste.
Mechanism of Thermal Desorption
Thermal desorption involves the application of heat to break down complex materials within the oil sludge, separating volatile components such as oils and gases from the non-volatile residues. The key concept is that different substances within the sludge have varying boiling points, allowing them to be selectively vaporized through the application of controlled heat. Once the volatile components are removed, the solid residuals can be safely disposed of or repurposed.
The process typically begins with the heating of oil sludge inside a thermal desorption system, where temperatures range from 200°C to 600°C. The temperature must be carefully controlled to ensure that the oil is recovered efficiently without causing thermal degradation or hazardous emissions. The volatile oil is then condensed into a liquid form, which can either be reused in industrial applications or treated further for refinement. The remaining solid material, often termed "spent catalyst" or "residue," is substantially reduced in volume and can be handled with fewer environmental risks.
Advantages of Using Thermal Desorption for Oil Sludge
Thermal desorption offers several benefits over traditional waste treatment methods, making it an increasingly attractive option for industries looking to address oil sludge contamination sustainably.
1. High Recovery of Oil
Thermal desorption efficiently recovers valuable oils from the sludge, making it economically viable. The recovered oil can be reused in various applications, such as fuel for industrial processes, lubricants, or even as feedstock for further refining. This oil recovery significantly reduces the environmental impact associated with petroleum waste, while also providing a revenue-generating resource for industries.
2. Reduction of Waste Volume
One of the key advantages of pyrolysis of oil sludge is its ability to reduce the volume of oil sludge. Through the separation of volatile components, the remaining solid residue is much smaller and more manageable. This reduction in waste volume decreases the need for landfills and helps minimize the long-term environmental burden of disposal.
3. Environmentally Safe Process
Thermal desorption, when properly conducted, minimizes the release of harmful emissions into the atmosphere. Modern thermal desorption units are equipped with sophisticated emission control systems, such as scrubbers and filters, to capture any potentially harmful gases produced during the heating process. This makes thermal desorption a cleaner and more environmentally friendly alternative to incineration or landfilling.
4. No Need for Chemical Additives
Unlike other methods that may require the addition of chemicals or solvents to break down oil sludge, thermal desorption operates solely through heat application. This results in a process that is free from the risks and costs associated with chemical treatments, making it more sustainable and cost-effective in the long term.
5. Versatility in Treating Various Sludge Types
Thermal desorption is highly versatile and can treat a wide range of oil sludge types, including those with varying levels of contamination. Whether the sludge contains crude oil, refined petroleum products, or other industrial oils, a thermal desorption unit can effectively process these materials to recover oil and reduce hazardous waste.
Applications and Industry Use
Thermal desorption is used across several industries where oil sludge accumulation is a significant issue. In the petroleum industry, it is employed to treat drilling wastes, tank bottom sludge, and other residual by-products generated during oil extraction and refining. The chemical industry also utilizes thermal desorption for processing waste materials that contain hydrocarbon residues.
In the power generation sector, where heavy oils are often used as fuel, thermal desorption provides an efficient method for recycling oil-based waste. Similarly, in the maritime industry, thermal desorption units are used to treat oily water and sludge produced by ships, ensuring that harmful residues are not released into the ocean.
Financial and Environmental Considerations
Implementing thermal desorption units provides an effective method of managing oil sludge while generating valuable oil products. However, the cost of establishing a thermal desorption system, particularly in large-scale operations, can be substantial. Factors such as the size of the facility, the nature of the waste, and the level of automation required for the desorption unit will influence the initial investment.
Nonetheless, the potential for revenue generation through oil recovery and the long-term savings on waste disposal make thermal desorption a financially viable option for many industries. Furthermore, the environmental benefits, including reduced landfilling, minimized contamination risks, and cleaner air quality, make thermal desorption an increasingly essential technology in the sustainable management of industrial waste.
Optimizing Thermal Desorption for Maximum Efficiency
To achieve optimal results, operators of thermal desorption units must focus on continuous improvement in both operational processes and maintenance practices. Proper control of temperature and residence time is crucial to maximizing oil recovery while minimizing energy consumption. Regular maintenance of the thermal desorption unit, including calibration of sensors and inspection of emission control devices, is also vital to ensure consistent performance and regulatory compliance.
In addition, operators should monitor the composition of the sludge to tailor the process to the specific characteristics of the waste. Some oil sludges may contain higher concentrations of heavy metals or other contaminants, which could affect the efficiency of the thermal desorption process. Adapting the operational parameters based on feedstock composition ensures higher yields and better overall performance.
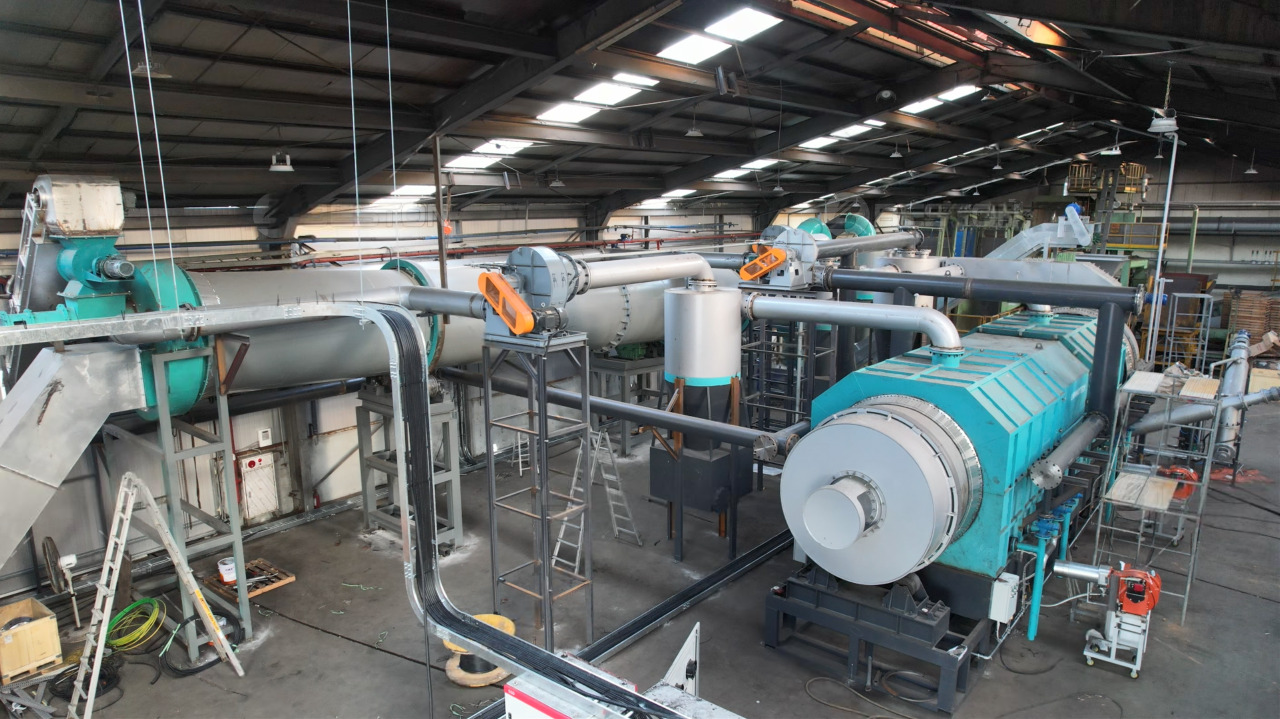
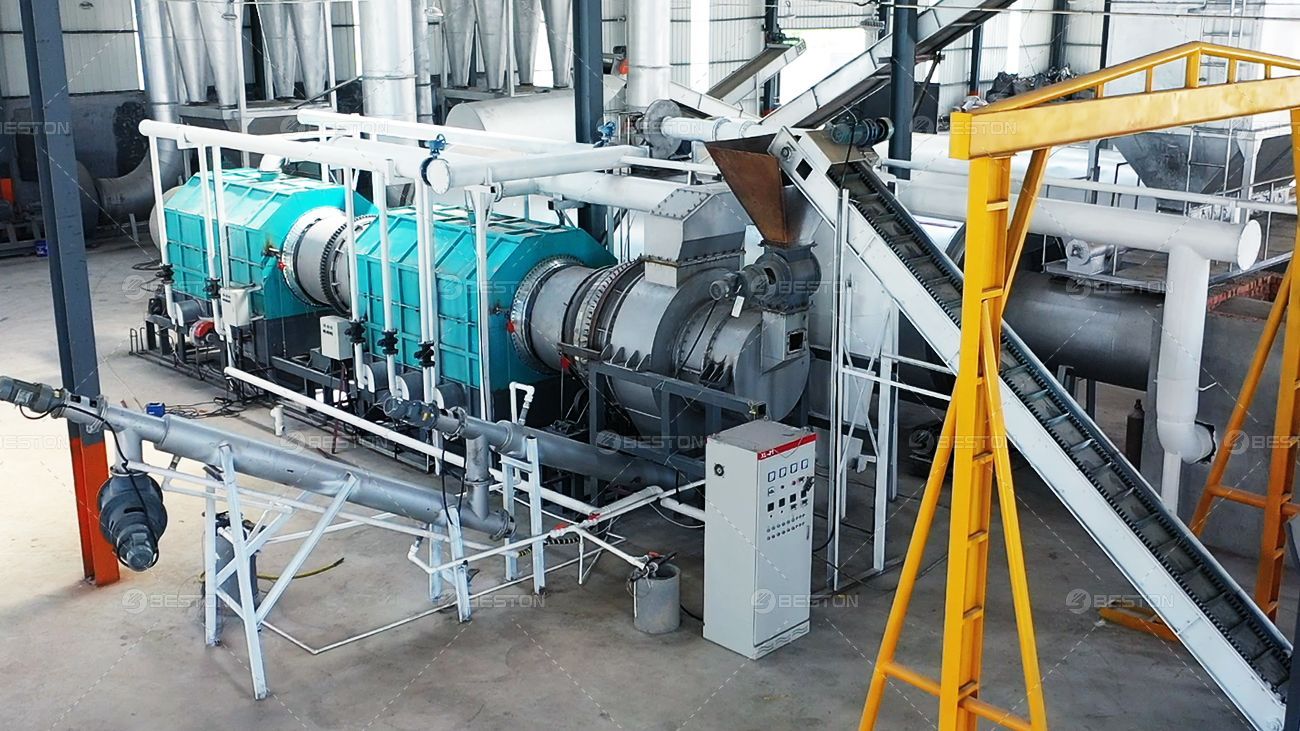
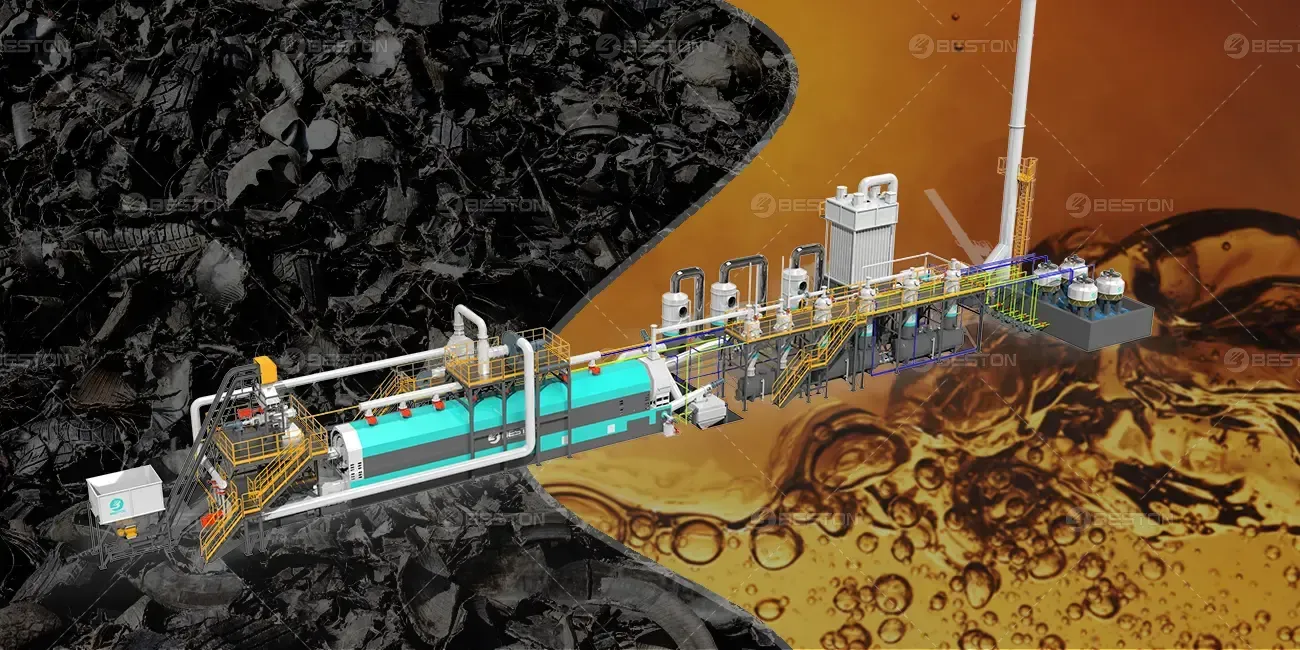