Key Factors Influencing Pyrolysis Plant Cost
This is a subtitle for your new post
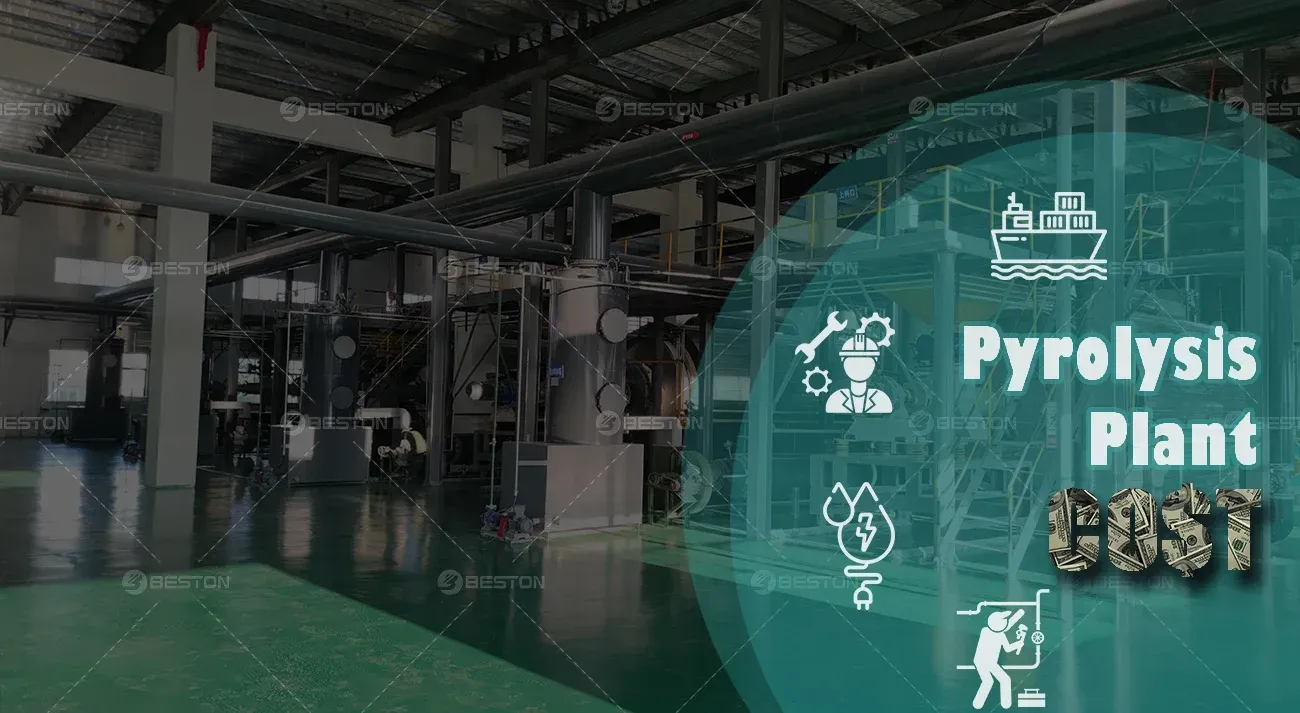
The financial outlay for establishing a pyrolysis plant is determined by multiple variables, each influencing the overall investment in distinct ways. Understanding these factors is crucial for prospective investors and businesses aiming to optimize their capital expenditure while ensuring operational efficiency. Whether it’s processing plastic, rubber, or organic waste, the cost structure of a pyrolysis plant is multifaceted and involves both fixed and operational expenditures.
1. Type and Scale of the Pyrolysis Plant
The type of pyrolysis plant chosen and its scale are among the primary determinants of the overall pyrolysis plant cost. Generally, pyrolysis systems are available in two main categories: batch and continuous. A batch system is typically more affordable in terms of initial investment due to its simpler design and operational structure. However, a continuous pyrolysis plant, which operates with higher efficiency and throughput, often comes at a higher price due to its more complex technology and design.
In terms of scale, larger plants that process a higher volume of waste tend to require more advanced equipment and greater infrastructure. As a result, larger capacity systems, while more expensive initially, can offer cost savings per unit of output in the long term. Conversely, smaller pyrolysis plants suited for pilot projects or smaller-scale operations will generally have a lower upfront cost but may require more frequent maintenance relative to their output capacity.
2. Raw Material Type and Feedstock Processing
The feedstock used in the pyrolysis process plays a crucial role in determining the cost of the plant. Different materials, such as plastic, tyres, biomass, or rubber, require specific processing equipment. For example, when dealing with tyres, a pyrolysis plant may need additional pre-treatment machinery to handle steel or other contaminants, which adds to the overall investment. Likewise, if the raw material requires additional drying, shredding, or sorting, this will increase the initial equipment cost and impact operational efficiency.
The chemical properties of the feedstock also affect the pyrolysis process itself, influencing the reactor design and required technology. Materials with higher moisture content or heterogeneous properties may demand more advanced reactors capable of handling irregularities, leading to higher construction and operational costs.
3. Reactor Design and Technology
The pyrolysis reactor is the heart of the plant, where the conversion of feedstock into useful by-products such as oil, gas, and carbon black takes place. Reactor design significantly impacts the pyrolysis plant cost due to factors such as the choice of material, size, and efficiency. Advanced reactors made from high-grade steel or with special linings for enhanced heat resistance tend to increase the initial capital investment.
Moreover, technology-driven features such as automated feeding systems, temperature control, and waste gas recovery systems all contribute to a higher upfront cost but can improve the long-term profitability and efficiency of the plant. Additionally, modern pyrolysis reactors with higher energy recovery capabilities can reduce overall operating costs, contributing to a quicker return on investment.
4. Emission Control and Environmental Compliance
One of the major ongoing costs of a pyrolysis plant is related to the management of emissions and compliance with environmental regulations. In many regions, the emission of volatile organic compounds (VOCs), particulates, and other potentially harmful gases is strictly controlled. The installation of scrubbers, filters, and gas treatment systems ensures that the plant meets environmental standards but adds to the capital expenditure.
While these technologies increase initial costs, they are indispensable for long-term operational viability. In some cases, the pyrolysis plant cost may also reflect the need to acquire permits and undergo environmental assessments to secure legal approval for operation.
5. Location and Infrastructure
The geographical location of the pyrolysis plant significantly affects the overall cost structure. Proximity to raw material sources, transportation networks, and access to utilities such as water and electricity can all influence the final investment. For example, setting up a pyrolysis facility in a remote or hard-to-access area may require additional costs for infrastructure development, including roads, power lines, and water supply systems.
Additionally, local labor costs, land acquisition expenses, and government incentives or taxes can influence the total capital outlay. In some areas, favorable environmental policies or tax breaks for renewable energy and waste processing technologies can help mitigate initial expenditures, making the location an important strategic consideration.
6. Operational Costs and Maintenance
Beyond the capital investment, operational costs play a critical role in determining the overall financial feasibility of a pyrolysis plant. Regular maintenance of equipment, energy consumption, and labor costs can all impact profitability over time. A plant that operates at high efficiency with low downtime will have lower long-term operational costs. Conversely, outdated or inefficient equipment may require more frequent maintenance and repairs, thus increasing the overall expense.
Energy costs, which typically account for a significant portion of the operating expenses, can be reduced by integrating energy recovery systems such as using pyrolysis gas to fuel the process. The more energy-efficient the plant, the lower the ongoing operational costs, leading to improved profitability over the plant's lifespan.
7. By-Product Marketability
The ability to effectively market and sell the by-products of pyrolysis – such as oil, gas, and carbon black – directly influences the overall profitability of the plant. A well-established supply chain and market for these products can offset a significant portion of the pyrolysis plant cost. For instance, pyrolysis oil can be sold as fuel or further refined into chemicals, while carbon black can be utilized in various industries, including manufacturing and construction.
If the market for these by-products is underdeveloped or fluctuates, the plant may struggle to achieve a solid return on investment, resulting in longer payback periods and increased financial pressure. Therefore, strategic market research and business planning are essential to ensuring that the products generated by the pyrolysis process have viable and stable demand.
Final Considerations
The overall pyrolysis plant cost is determined by a combination of the factors outlined above. Investors and plant operators must carefully assess each of these elements to ensure that they are making an informed decision based on both initial investment and long-term financial viability. By understanding the variables that affect pyrolysis plant costs, businesses can tailor their operations to optimize efficiency, reduce operating expenses, and ultimately achieve a higher return on investment.
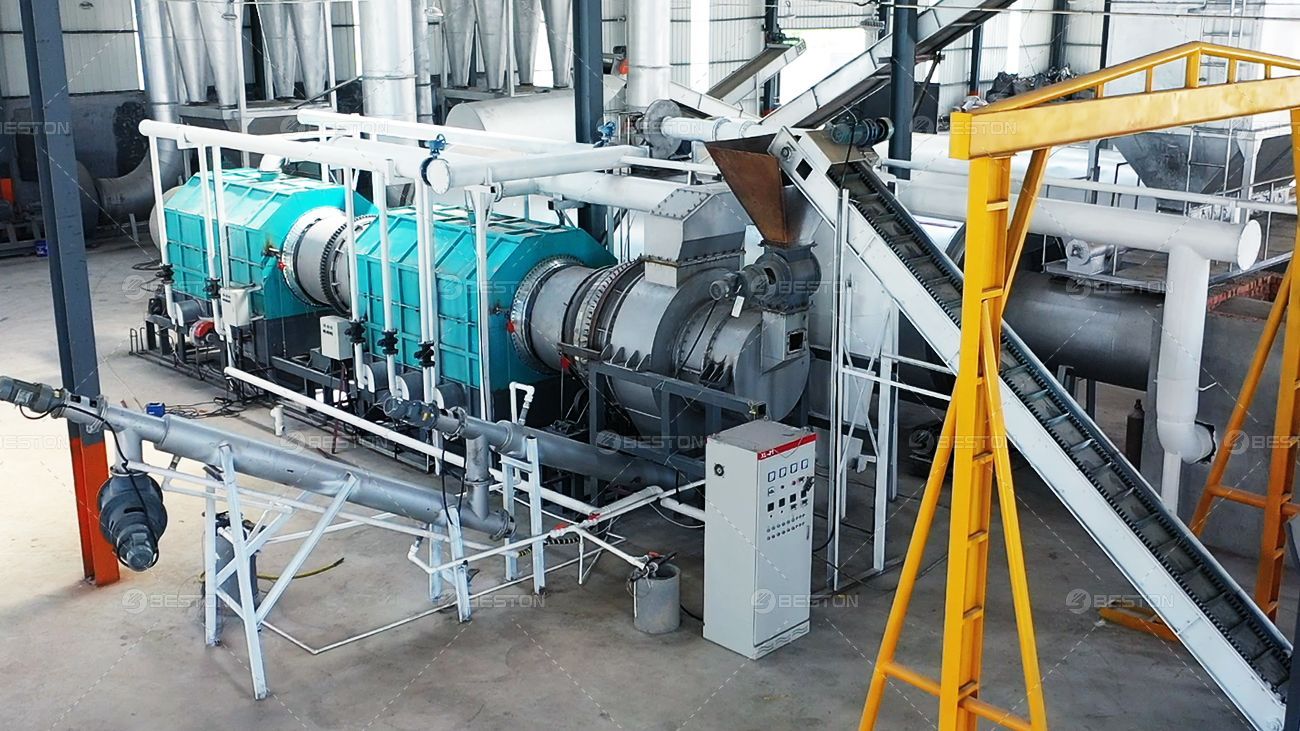
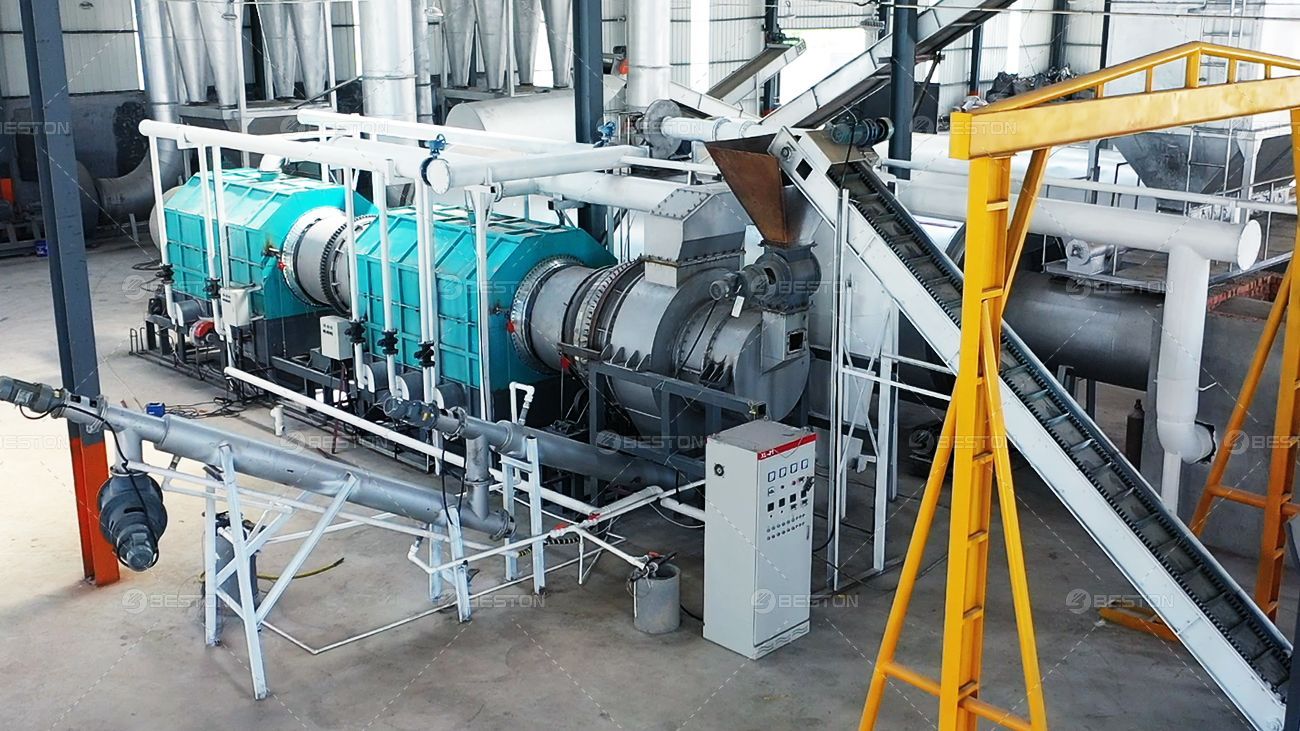
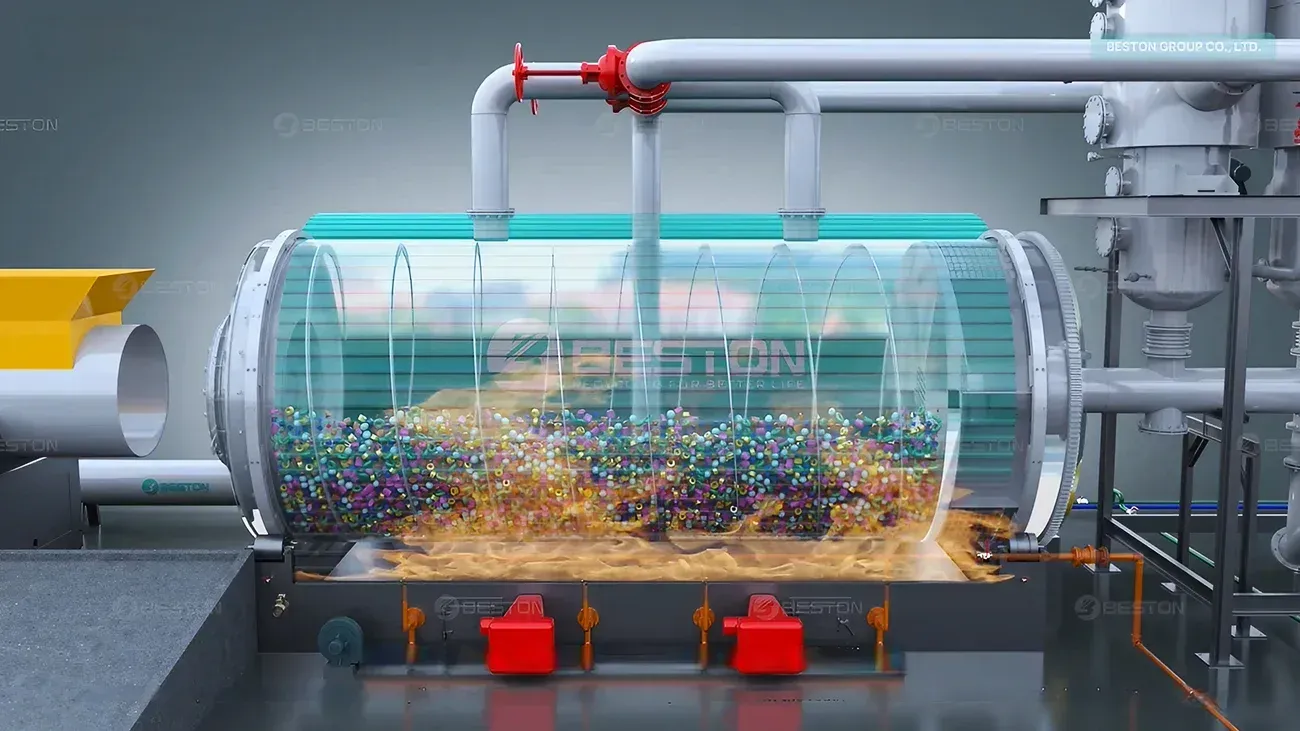