How to Improve Thermal Efficiency of Pyrolysis System
The pyrolysis system is a cornerstone of modern waste management and energy recovery technologies. By breaking down complex organic materials into simpler compounds through high-temperature processing, pyrolysis transforms waste into valuable byproducts such as biochar, pyrolysis oil, and syngas. However, optimizing the thermal efficiency of the pyrolysis system is crucial to maximizing energy recovery and ensuring economic viability. This article explores several strategies to enhance the thermal efficiency of pyrolysis systems, delving into technological innovations, process optimizations, and material considerations.
Understanding Pyrolysis System Dynamics
To improve the thermal efficiency of a pyrolysis system , it is imperative to understand the fundamental principles governing its operation. The pyrolysis process involves heating organic materials in the absence of oxygen, leading to their decomposition into volatile gases and solid residues. The efficiency of this process is determined by the rate and completeness of the thermal decomposition, which is influenced by several factors, including reactor design, heating rate, feedstock properties, and thermal insulation.
Advanced Reactor Design
Reactor design plays a pivotal role in determining the thermal efficiency of a pyrolysis system. Several reactor types are commonly used, each with unique advantages and limitations:
- Fixed-Bed Reactors: These reactors are simple in design and operation but often suffer from poor heat transfer efficiency. Optimizing the packing of the feedstock and enhancing heat conduction through the bed can improve efficiency.
- Fluidized-Bed Reactors: Known for their excellent heat transfer characteristics, fluidized-bed reactors ensure uniform heating of the feedstock. By optimizing the fluidization velocity and particle size, the thermal efficiency can be significantly enhanced.
- Rotary Kiln Reactors: These reactors offer continuous operation and good mixing of feedstock. The inclination angle and rotation speed of the kiln can be adjusted to improve the contact between the material and the heat source.
Optimizing Heating Rate and Temperature
The heating rate and process temperature are critical parameters influencing the pyrolysis process. A rapid heating rate can increase the yield of volatile gases, while a slower rate may favor the production of char. Striking a balance between these rates is essential to maximize the desired product yield.
Moreover, operating at an optimal temperature range is crucial. Higher temperatures generally enhance the conversion efficiency but may also increase energy consumption. Implementing advanced control systems to monitor and adjust the temperature in real-time can help maintain optimal conditions, thereby improving thermal efficiency.

Feedstock Preparation and Characteristics
The properties of the feedstock significantly impact the efficiency of a pyrolysis system. Key factors to consider include moisture content, particle size, and composition:
- Moisture Content: High moisture content in the feedstock can lead to increased energy consumption as more heat is required to evaporate the water. Pre-drying the feedstock can reduce moisture levels, thereby enhancing thermal efficiency.
- Particle Size: Smaller particle sizes facilitate better heat transfer and faster decomposition rates. However, excessively fine particles may lead to agglomeration and reduced gas flow. Achieving an optimal particle size distribution is crucial.
- Composition: The chemical composition of the feedstock affects its pyrolysis behavior. Understanding the composition allows for adjustments in process parameters to maximize efficiency and product yield.
Enhancing Thermal Insulation
Effective thermal insulation is vital to minimizing heat losses in a small scale pyrolysis unit. Insulating materials should be selected based on their thermal resistance, durability, and cost-effectiveness. Common insulation materials include ceramic fibers, mineral wool, and refractory bricks. Incorporating multi-layer insulation systems can further reduce heat losses and improve overall efficiency.
Heat Recovery and Energy Integration
Integrating heat recovery systems within the pyrolysis process can significantly enhance thermal efficiency. Capturing waste heat from the exhaust gases and using it to preheat the feedstock or generate steam for auxiliary processes can reduce overall energy consumption. Technologies such as heat exchangers and recuperators are commonly employed for this purpose.
Additionally, energy integration with other industrial processes can create synergistic effects. For example, the heat generated from pyrolysis can be used in adjacent processes, such as drying or electricity generation, thereby maximizing the utilization of available energy resources.
Utilizing Catalyst and Additives
Catalysts and additives can be employed to modify the pyrolysis process and enhance thermal efficiency. Catalysts can lower the activation energy required for decomposition, allowing the process to occur at lower temperatures. This reduces energy consumption while increasing product yield.
Moreover, additives can be used to improve the quality of the pyrolysis products, such as enhancing the calorific value of syngas or the quality of biochar. Selecting the appropriate catalyst or additive requires a thorough understanding of the feedstock and desired product characteristics.
Automation and Process Control
Implementing advanced automation and process control systems can significantly improve the thermal efficiency of pyrolysis systems. Real-time monitoring and control of process parameters, such as temperature, pressure, and feedstock flow rate, ensure optimal operating conditions are maintained. Advanced control algorithms can adjust these parameters dynamically, responding to changes in feedstock properties or environmental conditions.
Furthermore, data analytics and machine learning can be utilized to analyze historical process data and identify patterns that lead to efficiency improvements. Predictive maintenance, enabled by these technologies, can also minimize downtime and ensure consistent performance.
Concluding Remarks
Enhancing the thermal efficiency of a pyrolysis system is a multifaceted challenge that requires a holistic approach. By optimizing reactor design, process parameters, feedstock characteristics, and thermal management strategies, significant improvements can be achieved. The integration of heat recovery systems and the use of catalysts further contribute to maximizing energy recovery and product yield. Finally, the adoption of advanced automation and control technologies ensures that pyrolysis systems operate at peak efficiency, paving the way for sustainable waste management and energy recovery solutions.
Through continuous innovation and optimization, the potential of pyrolysis as a transformative technology in the circular economy can be fully realized, driving progress toward a more sustainable and resource-efficient future.
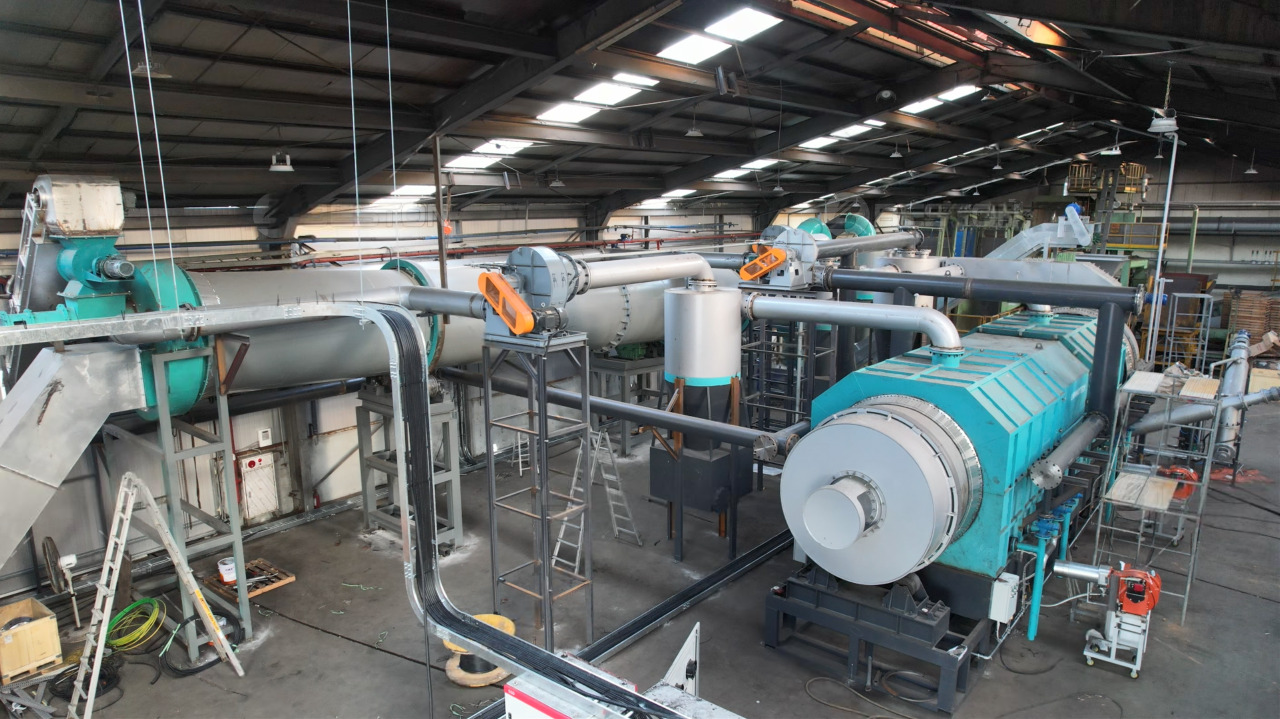
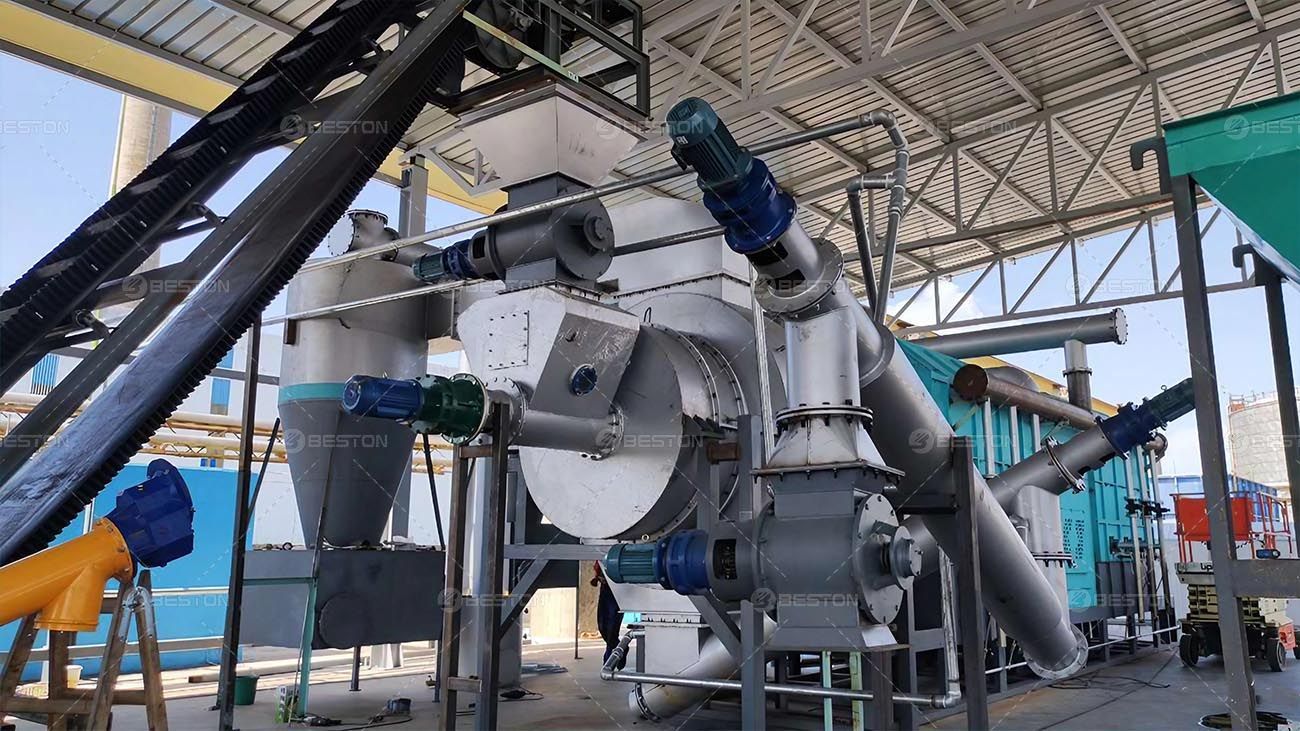
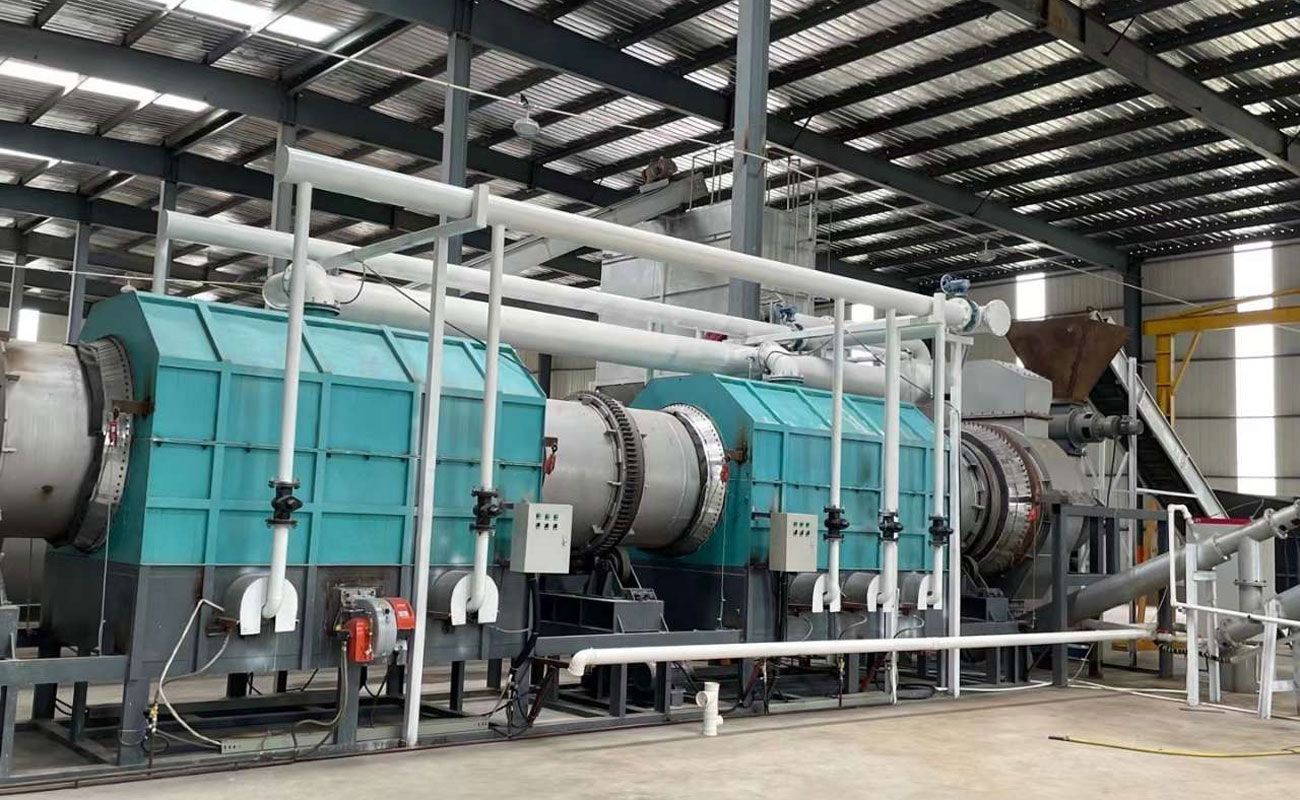