5 Strategies for Producing High-Quality Coconut Shell Charcoal
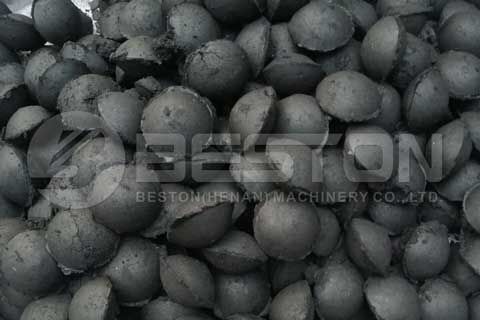
Introduction
The production of high-quality coconut shell charcoal is a sophisticated process that demands precision and attention to detail. Coconut shell charcoal, derived from the shells of coconuts, is a valuable resource due to its superior characteristics, including high energy density and low ash content. The effectiveness of this process relies heavily on the use of advanced technologies, particularly the coconut shell charcoal making machine. This article outlines five key strategies for optimizing the production of premium coconut shell charcoal.
1. Optimal Feedstock Preparation
The quality of the final coconut shell charcoal largely depends on the preparation of the feedstock. Properly processed coconut shells ensure uniformity in the charcoal production process and enhance the quality of the resulting product. The preparation involves several critical steps:
Cleaning and Sorting
Initially, the coconut shells should be cleaned to remove any residual organic material, such as fibers or pulp. Residual impurities can affect the burning process and reduce the efficiency of the charcoal. Sorting the shells to ensure uniform size and removing any foreign materials are essential for achieving a consistent product.
Drying
After cleaning, the coconut shells need to be thoroughly dried. Moisture content in the shells can lead to inefficient pyrolysis and result in low-quality charcoal. The shells should be dried in a well-ventilated area or using a controlled drying system to reach an optimal moisture level before pyrolysis.
2. Efficient Pyrolysis Process
Pyrolysis, the thermal decomposition of organic material in the absence of oxygen, is a pivotal step in coconut shell charcoal machine. The efficiency and quality of the charcoal depend on the conditions under which pyrolysis is conducted.
Temperature Control
Maintaining precise temperature control during pyrolysis is crucial. The optimal temperature range for producing high-quality coconut shell charcoal is typically between 500°C and 700°C. At this temperature, the shells undergo complete carbonization, resulting in a product with high carbon content and minimal volatile matter. Variations in temperature can lead to incomplete pyrolysis and affect the final quality of the charcoal.
Residence Time
The duration of the pyrolysis process, or residence time, also impacts the quality of the charcoal. Adequate residence time ensures that the shells are fully carbonized. However, excessively long pyrolysis times can lead to over-carbonization and the formation of excess ash. Balancing the residence time with the temperature settings ensures optimal charcoal production.
3. Utilization of Advanced Charcoal Making Machines
The use of modern coconut shell charcoal making machines significantly enhances the efficiency and consistency of the production process. These machines are designed to optimize various aspects of charcoal production, including:
Automation
Modern charcoal making machines often feature automation capabilities that streamline the production process. Automation reduces human error and ensures consistent processing conditions, leading to uniform charcoal quality. Features such as automated temperature control and timing mechanisms are integral to achieving high-quality output.
Efficiency
Advanced machines are engineered for high efficiency, maximizing the yield of charcoal while minimizing energy consumption and waste. Features such as improved insulation, efficient heating systems, and advanced combustion chambers contribute to the overall effectiveness of the production process.
4. Post-Pyrolysis Treatment
Post-pyrolysis treatment plays a crucial role in enhancing the quality of coconut shell charcoal. Proper treatment processes can improve the physical and chemical properties of the charcoal, making it suitable for various applications.
Screening and Crushing
After pyrolysis, the charcoal is typically screened to remove any oversized particles and impurities. Crushing the charcoal into uniform granules ensures consistency in size and enhances its usability in applications such as filtration and as a fuel. The size of the crushed charcoal can be adjusted based on its intended use.
Activation
For certain applications, particularly in filtration and adsorption, the charcoal may undergo activation. Activation involves treating the charcoal with an oxidizing agent, such as steam or carbon dioxide, to enhance its surface area and adsorption capacity. This process increases the charcoal's effectiveness in applications that require high porosity and surface area.
5. Quality Control and Testing
Implementing rigorous quality control measures is essential for ensuring the production of high-quality coconut shell charcoal. Testing and monitoring throughout the production process help maintain consistent quality and meet industry standards.
Physical and Chemical Analysis
Regular physical and chemical analysis of the charcoal is necessary to assess its quality. Parameters such as carbon content, ash content, moisture level, and volatile matter should be measured to ensure the charcoal meets the required specifications. Testing laboratories can provide detailed analyses that guide adjustments in the production process.
Continuous Monitoring
Continuous monitoring of the charcoal production machine helps identify and rectify any deviations from optimal conditions. Monitoring systems can track variables such as temperature, pressure, and residence time, providing real-time data that supports quality control efforts. Implementing feedback mechanisms allows for immediate corrections and improvements.
Conclusion
Producing high-quality coconut shell charcoal involves a multifaceted approach that integrates optimal feedstock preparation, efficient pyrolysis, advanced charcoal making machines, effective post-pyrolysis treatment, and stringent quality control. By adhering to these strategies, producers can enhance the performance and consistency of their coconut shell charcoal, making it a valuable resource for various applications. The application of these techniques ensures that the final product not only meets industry standards but also stands out for its superior quality and efficiency.
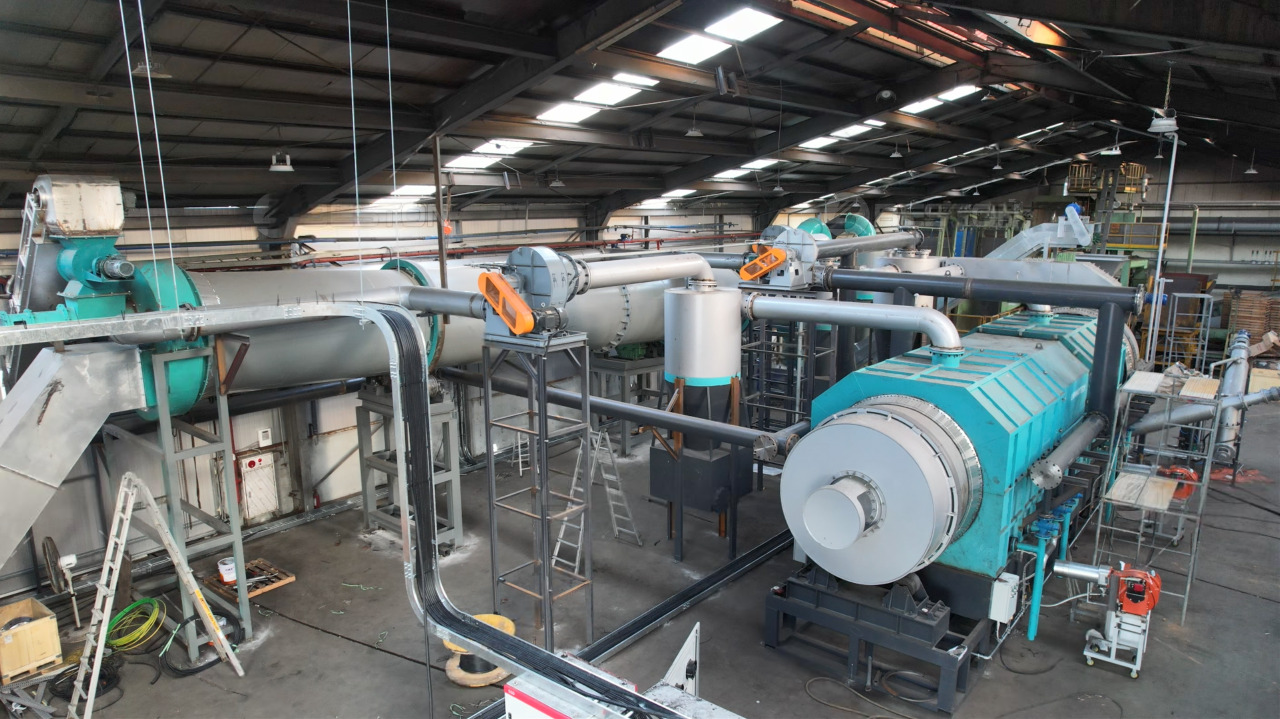
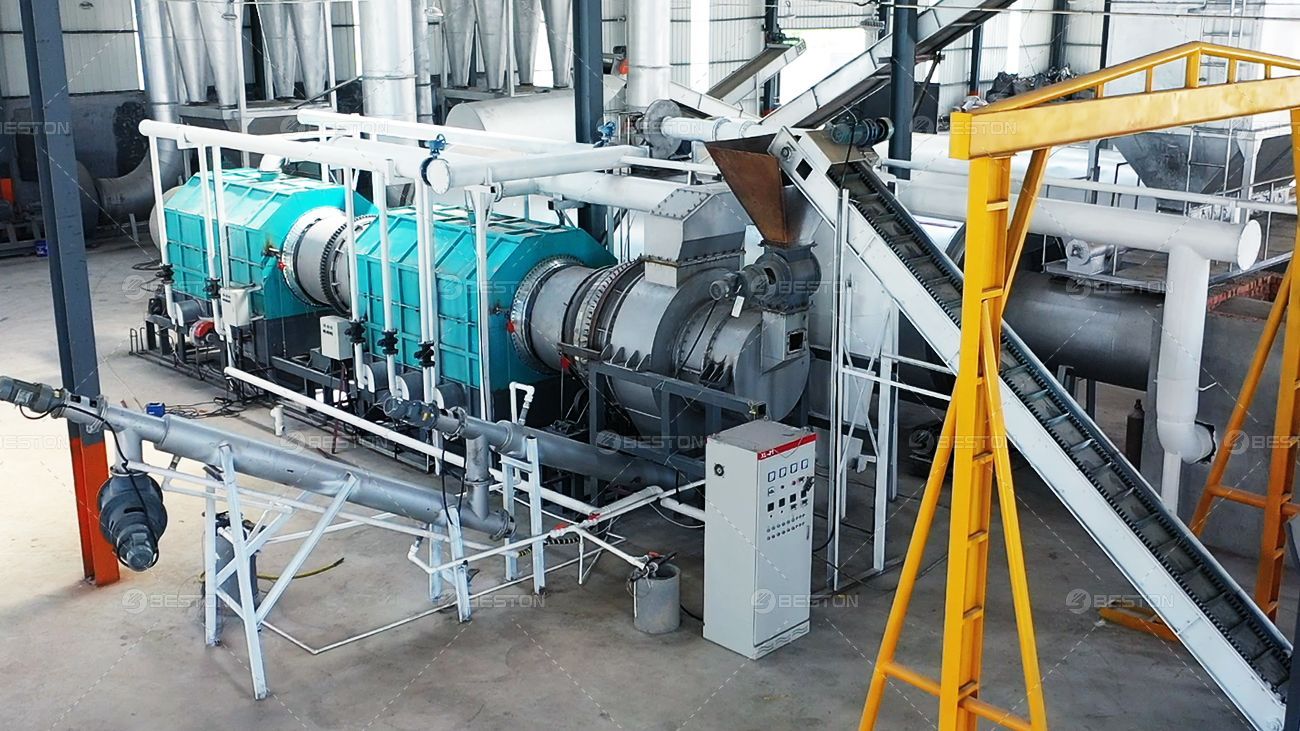
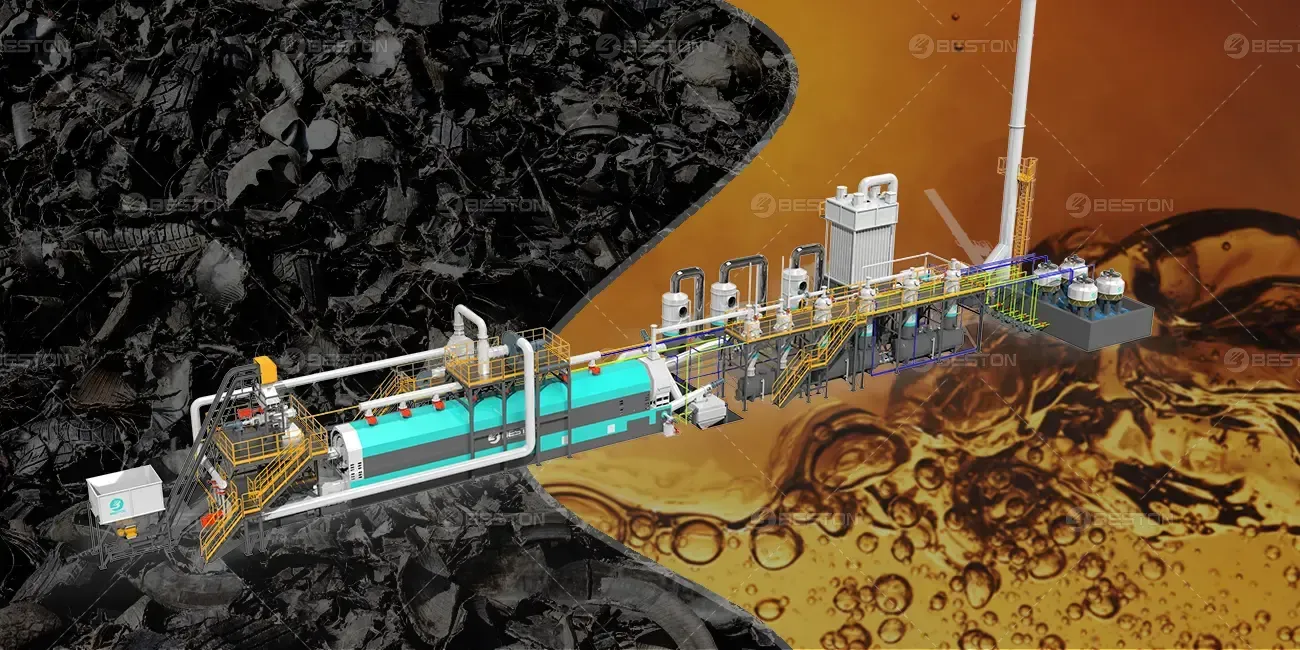