Pyrolysis Technology: Solving the Problem of Plastic Degradation
This is a subtitle for your new post
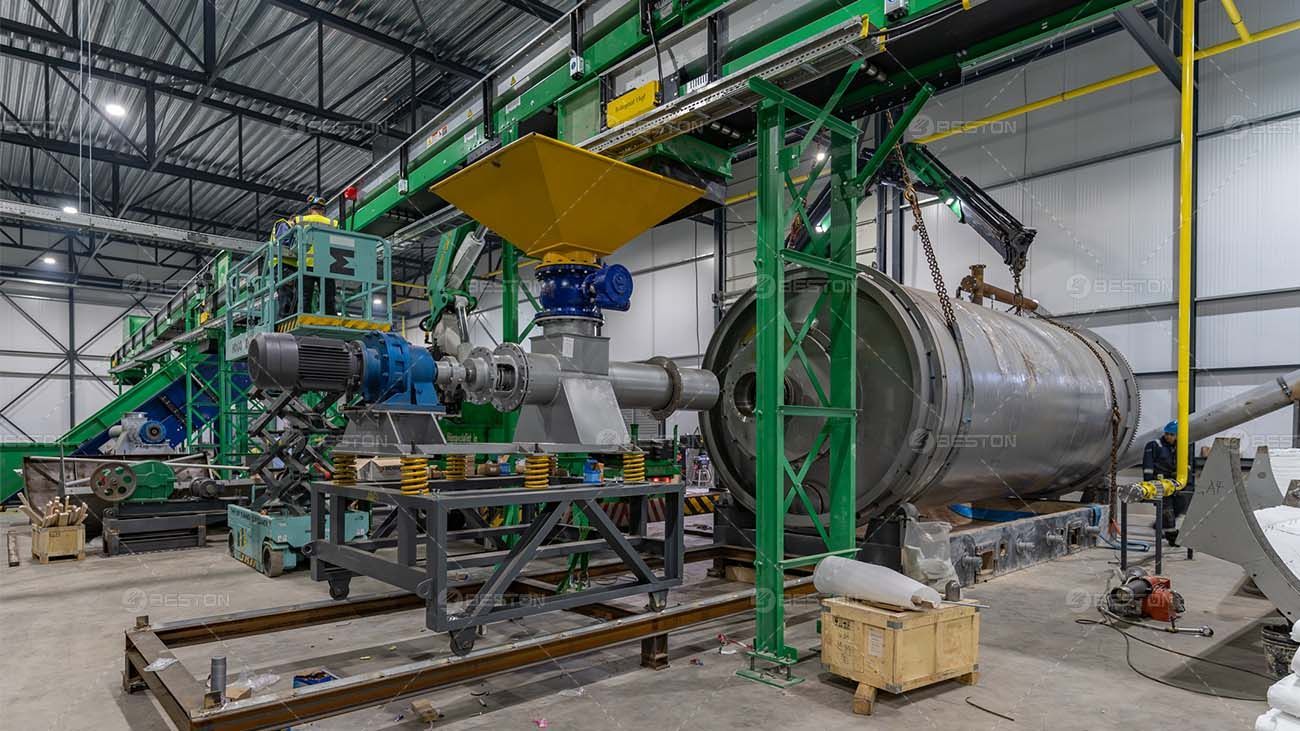
Plastic pollution has emerged as a global environmental crisis, with widespread implications for ecosystems and human health. Conventional methods of plastic disposal, including landfilling and incineration, contribute to environmental degradation and resource depletion. However, the advent of pyrolysis technology offers a promising solution to this pressing issue. By harnessing the principles of thermochemical decomposition, plastic pyrolysis equipment enables the conversion of plastic waste into valuable resources, mitigating environmental harm and fostering resource sustainability.
Understanding Plastic Degradation
Plastic degradation refers to the deterioration of plastic materials over time, leading to the release of harmful pollutants into the environment. This process occurs through various mechanisms, including photodegradation, mechanical abrasion, and chemical breakdown. As plastics accumulate in landfills and oceans, they pose significant risks to wildlife, marine ecosystems, and human populations. Addressing the challenge of plastic degradation requires innovative approaches that minimize environmental impact and maximize resource recovery.
The Role of Pyrolysis Technology
Pyrolysis technology offers a transformative solution to the problem of plastic degradation. At its core, pyrolysis involves the thermal decomposition of organic materials in the absence of oxygen, leading to the generation of valuable products such as liquid fuels, gases, and char. Plastic pyrolysis equipment utilizes this principle to convert plastic waste into useful commodities through controlled heating and catalytic processes. By breaking down complex polymer chains into simpler hydrocarbons, pyrolysis technology enables the recovery of energy and raw materials from plastic waste streams, thereby reducing reliance on fossil fuels and mitigating environmental pollution.
Operational Mechanism
The operational mechanism of plastic pyrolysis equipment entails several key steps:
- Feedstock Preparation: Plastic waste is collected and sorted to remove contaminants such as metals and non-recyclable materials.
- Feedstock Heating: The prepared plastic feedstock is introduced into the pyrolysis reactor, where it undergoes thermal decomposition at elevated temperatures ranging from 300°C to 800°C.
- Volatile Gasification: As the plastic feedstock heats up, volatile gases are released, including hydrocarbons, carbon monoxide, and hydrogen. These gases are routed through a series of condensers and separators to recover valuable liquid fuels and chemicals.
- Residue Formation: The remaining solid residue, known as char or pyrolysis coke, is collected and can be further processed for applications such as carbon black production or soil amendment.
- Gas Treatment: Any remaining gases, including non-condensable hydrocarbons and impurities, are treated to remove pollutants before being released into the atmosphere or utilized for energy generation.

Key Advantages
1. Environmental Sustainability
Plastic pyrolysis technology offers significant environmental benefits by diverting plastic waste from landfills and reducing greenhouse gas emissions associated with conventional disposal methods. By converting plastic waste into valuable resources such as fuels and chemicals, pyrolysis mitigates environmental pollution and contributes to a circular economy model wherein waste is viewed as a resource rather than a liability.
2. Resource Recovery
One of the primary advantages of plastic pyrolysis technology is its ability to recover energy and raw materials from plastic waste streams. The liquid fuels produced through pyrolysis, often referred to as pyrolysis oil or synthetic crude, can be used as feedstock for industrial processes or upgraded into higher-value products such as transportation fuels or specialty chemicals. Additionally, the char residue generated during pyrolysis can be utilized in various applications, including soil remediation and carbon sequestration.
3. Waste Reduction
By converting plastic waste into valuable products, pyrolysis technology helps alleviate the burden of plastic pollution on the environment and human health. Instead of accumulating in landfills or polluting oceans, plastic waste can be transformed into useful commodities, thereby reducing the demand for virgin materials and minimizing the environmental footprint of plastic production and consumption.
4. Versatility and Scalability
Plastic pyrolysis technology is highly versatile and scalable, making it suitable for a wide range of applications and waste streams. Pyrolysis equipment can be customized to process different types of plastic waste, including polyethylene, polypropylene, polystyrene, and polyethylene terephthalate (PET). Furthermore, pyrolysis plants can be scaled up or down to accommodate varying feedstock volumes and operational requirements, making them adaptable to diverse geographical locations and industrial settings.
Emerging Trends and Innovations
The field of plastic pyrolysis is continually evolving, driven by technological advancements and market dynamics. Several trends and innovations are shaping the future of plastic pyrolysis technology:
1. Advanced Catalytic Pyrolysis
Catalytic pyrolysis involves the use of catalysts to enhance the efficiency and selectivity of the pyrolysis process. Advanced catalysts, such as zeolites, metal oxides, and supported nanoparticles, enable higher conversion rates and yield of valuable products while minimizing undesirable byproducts such as char and coke. Catalytic pyrolysis holds promise for improving the economics and environmental performance of plastic pyrolysis technology.
2. Integration with Renewable Energy Sources
The integration of plastic pyrolysis technology with renewable energy sources such as solar, wind, and biomass offers opportunities for sustainable and decentralized waste-to-energy solutions. By coupling pyrolysis plants with renewable energy generation facilities, it is possible to reduce reliance on fossil fuels and mitigate greenhouse gas emissions associated with energy production and waste management.
3. Circular Economy Initiatives
Plastic pyrolysis technology plays a crucial role in advancing circular economy initiatives aimed at closing the loop on plastic waste. By converting post-consumer and post-industrial plastic waste into feedstock for new products and materials, pyrolysis contributes to the circularity of plastics, thereby reducing the need for virgin materials and minimizing environmental impact throughout the product lifecycle.
4. Policy Support and Market Incentives
Government policies and market incentives are driving the adoption of plastic pyrolysis technology as part of broader strategies to address plastic pollution and promote sustainable development. Initiatives such as extended producer responsibility (EPR), plastic waste management regulations, and carbon pricing mechanisms create favorable conditions for investment in pyrolysis infrastructure and incentivize the transition towards a circular plastics economy.
Conclusion
Plastic pyrolysis technology represents a transformative approach to addressing the challenge of plastic degradation and pollution. By converting plastic waste into valuable resources through thermochemical decomposition, pyrolysis technology offers environmental, economic, and social benefits. As the field continues to evolve and innovate, plastic pyrolysis holds promise as a key enabler of a sustainable and circular economy wherein plastic waste is viewed as a valuable resource rather than a disposable nuisance.
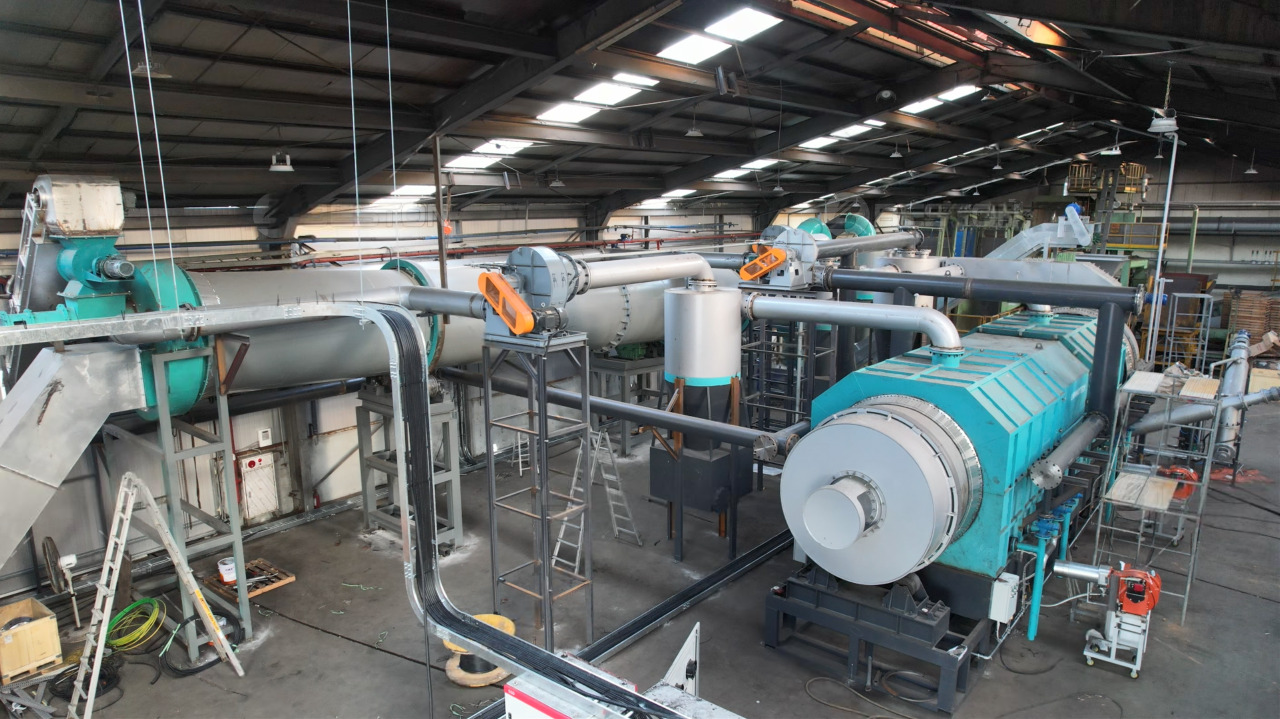
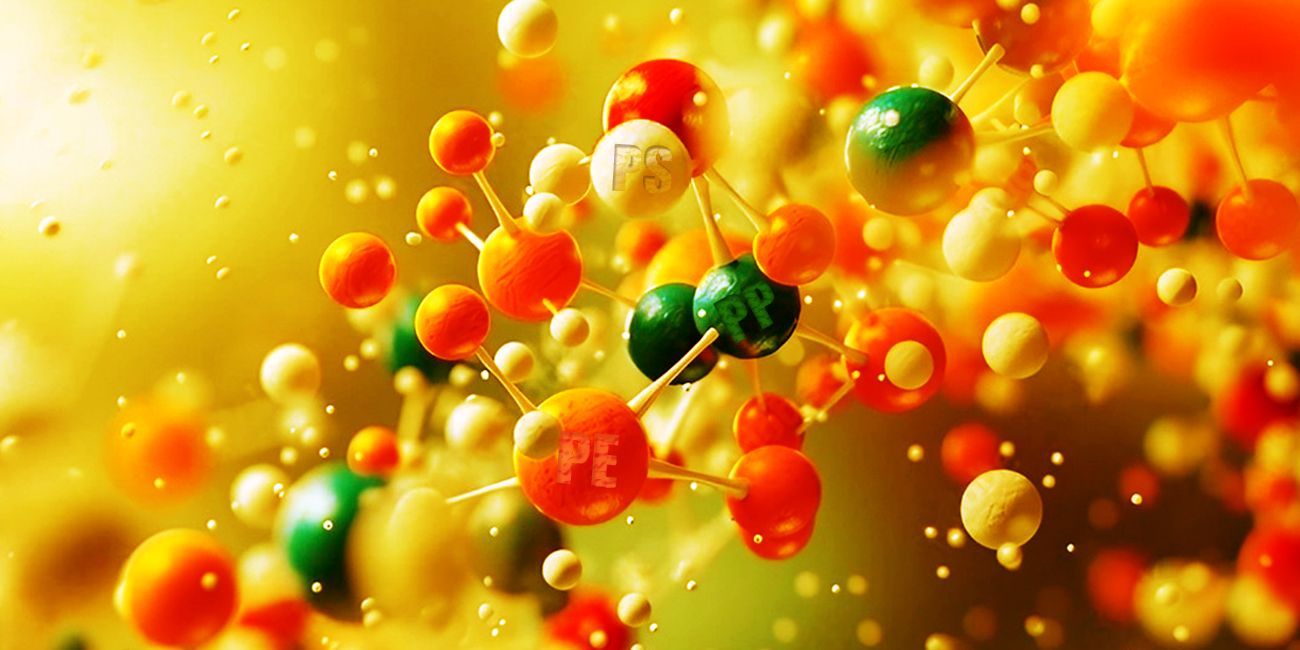