Improving the Thermal Efficiency of Biochar Making Machine
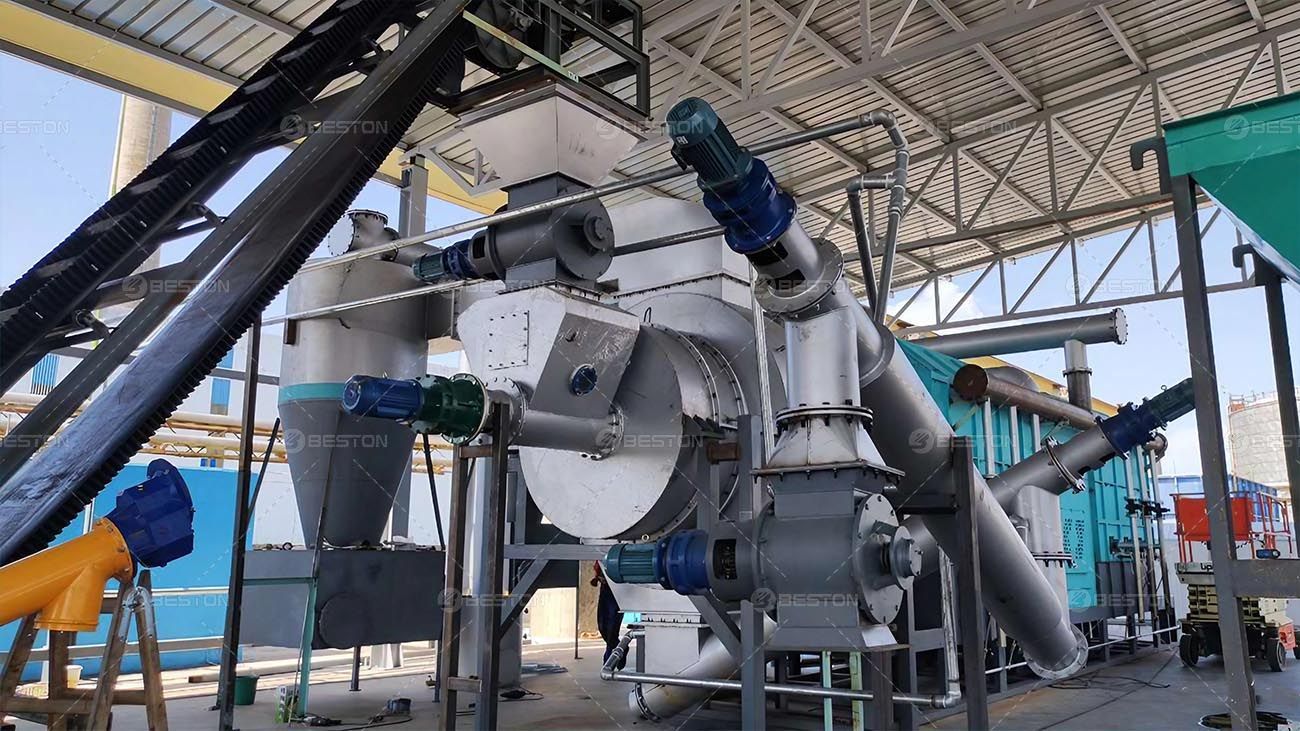
Biochar production, a process that involves converting organic material into carbon-rich biochar using pyrolysis, has gained significant attention for its environmental benefits. A biochar making machine plays a pivotal role in transforming biomass into biochar by utilizing heat in an oxygen-limited environment. However, the efficiency of this machine can greatly influence both the economic and environmental viability of the process. Improving the thermal efficiency of a biochar making machine can reduce energy consumption, increase output, and lower operational costs, all of which contribute to the sustainability of biochar production. Several strategies can be employed to enhance the thermal efficiency of these machines.
1. Optimizing the Pyrolysis Temperature
The pyrolysis process in a biochar making machine is highly sensitive to temperature. Typically, the conversion of biomass to biochar requires a temperature range of 400°C to 700°C. Maintaining the right temperature is crucial for maximizing biochar yield while minimizing energy consumption. The key to improving thermal efficiency lies in ensuring that the machine operates within an optimal temperature range.
- Automated Temperature Control: Implementing automated temperature control systems in the biochar making machine can help maintain consistent heat levels. This ensures that the temperature does not fluctuate excessively, which could lead to energy waste.
- Heat Retention: Improving insulation within the machine can prevent heat loss and reduce the need for external energy sources to maintain temperature. High-quality refractory materials and insulating linings can be used in the furnace or pyrolysis chamber to reduce thermal losses.
2. Improving Biomass Feeding Mechanism
The feeding mechanism of biomass into the biochar making machine is another crucial factor in improving thermal efficiency. The rate at which biomass is fed into the machine influences the heat distribution and the efficiency of the pyrolysis process.
- Consistent Feed Rate: Maintaining a consistent feed rate ensures that biomass is evenly distributed, allowing for uniform heating. Irregular feeding can cause fluctuations in temperature, leading to inefficient heat use and inconsistent biochar production.
- Pre-Treatment of Biomass: Pre-treating biomass before it enters the machine can also improve thermal efficiency. Drying the biomass reduces its moisture content, which otherwise consumes a considerable amount of energy during pyrolysis. The use of mechanical dryers or solar drying can significantly improve the process's energy balance.
3. Utilizing Waste Heat Recovery Systems
A significant portion of the energy used in the pyrolysis process is in the form of waste heat. Many biochar making machines release excess heat during operation, which is often not captured or reused. Implementing a waste heat recovery system can significantly improve the thermal efficiency of the machine.
- Heat Exchanger Systems: Installing heat exchangers within the biochar making machine allows for the recovery of waste heat. This recovered heat can be redirected back into the system to maintain the desired pyrolysis temperature, reducing the need for external fuel.
- Syngas Utilization: The syngas produced during the pyrolysis process can be used as an alternative fuel source. By capturing and utilizing this syngas, the biochar making machine can operate more efficiently without relying heavily on external energy sources.
4. Enhancing Airflow Management
The airflow within the biochar making machine significantly impacts the combustion and pyrolysis processes. Proper airflow management ensures that the biomass receives adequate oxygen during the process, which helps in maintaining the necessary heat levels.
- Optimized Air Distribution: Installing adjustable vents or fans can ensure that the airflow is evenly distributed throughout the biomass. This prevents localized overheating or underheating, thus enhancing the overall thermal efficiency.
- Oxygen Control: While pyrolysis occurs in an oxygen-limited environment, some level of controlled oxygen is necessary to aid in the combustion of gases, improving the overall thermal balance. By adjusting the oxygen levels carefully, the biochar making machine can achieve more efficient combustion, which directly contributes to better thermal efficiency.
5. Enhancing Machine Design and Materials
The design and construction of the biochar making machine can also influence its thermal efficiency. Incorporating advanced materials and design features can significantly reduce heat loss and improve the overall efficiency of the pyrolysis process.
- Advanced Insulation Materials: The use of advanced, high-performance insulation materials for the outer shell and internal components of the machine minimizes heat loss. Insulation materials such as ceramic wool or calcium silicate boards can be applied to ensure maximum heat retention.
- Optimized Chamber Design: The design of the pyrolysis chamber should facilitate efficient heat distribution. A well-designed chamber will allow for even heat distribution, reducing hot spots and ensuring uniform biochar production. Circular or conical chambers tend to have better heat distribution compared to irregularly shaped ones.
6. Implementing Automated Monitoring and Control Systems
Automating the monitoring and control systems of a biochar making machine can help in fine-tuning the pyrolysis process for optimal thermal efficiency. Sensors and control systems can track key variables such as temperature, pressure, and gas composition, allowing for real-time adjustments.
- Data-Driven Decision Making: By using sensors to collect data throughout the pyrolysis process, operators can identify inefficiencies and adjust the parameters to optimize performance. For example, real-time temperature monitoring can help prevent overheating or underheating, which could lead to energy waste.
- Preventing Equipment Failures: Automated systems can also predict potential equipment failures, reducing downtime and ensuring that the biochar making machine operates at peak thermal efficiency without interruption.
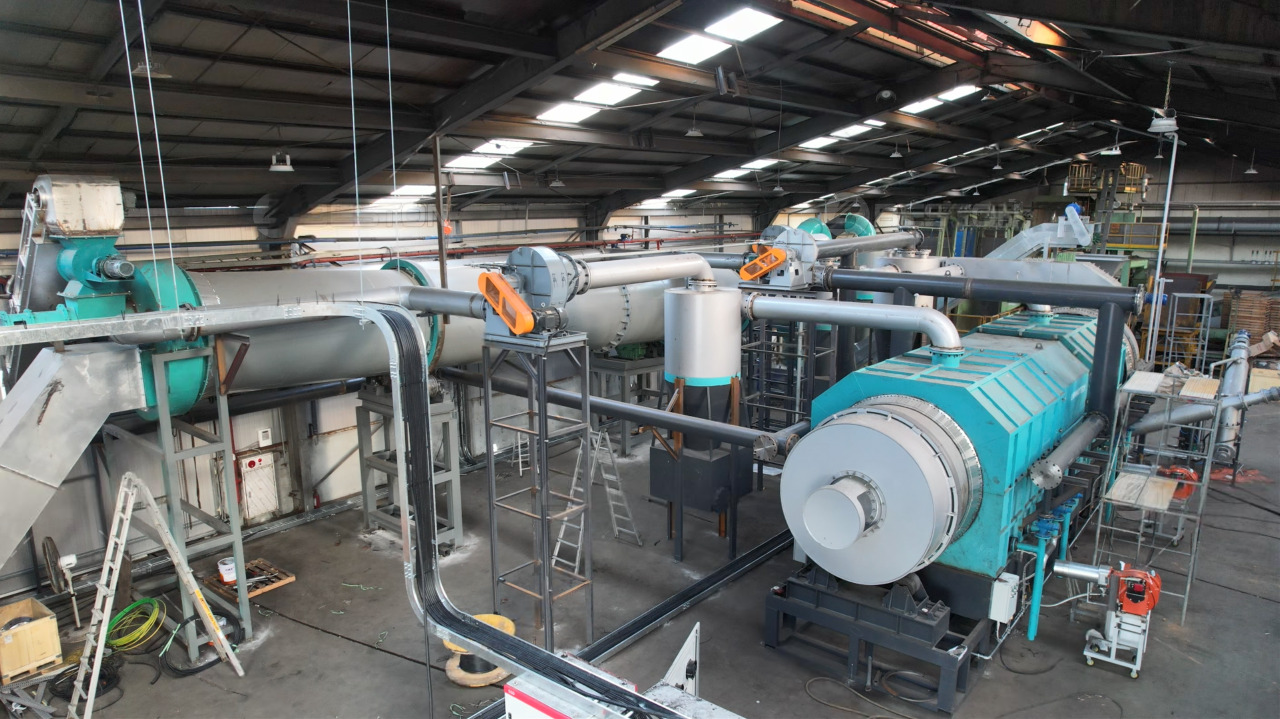
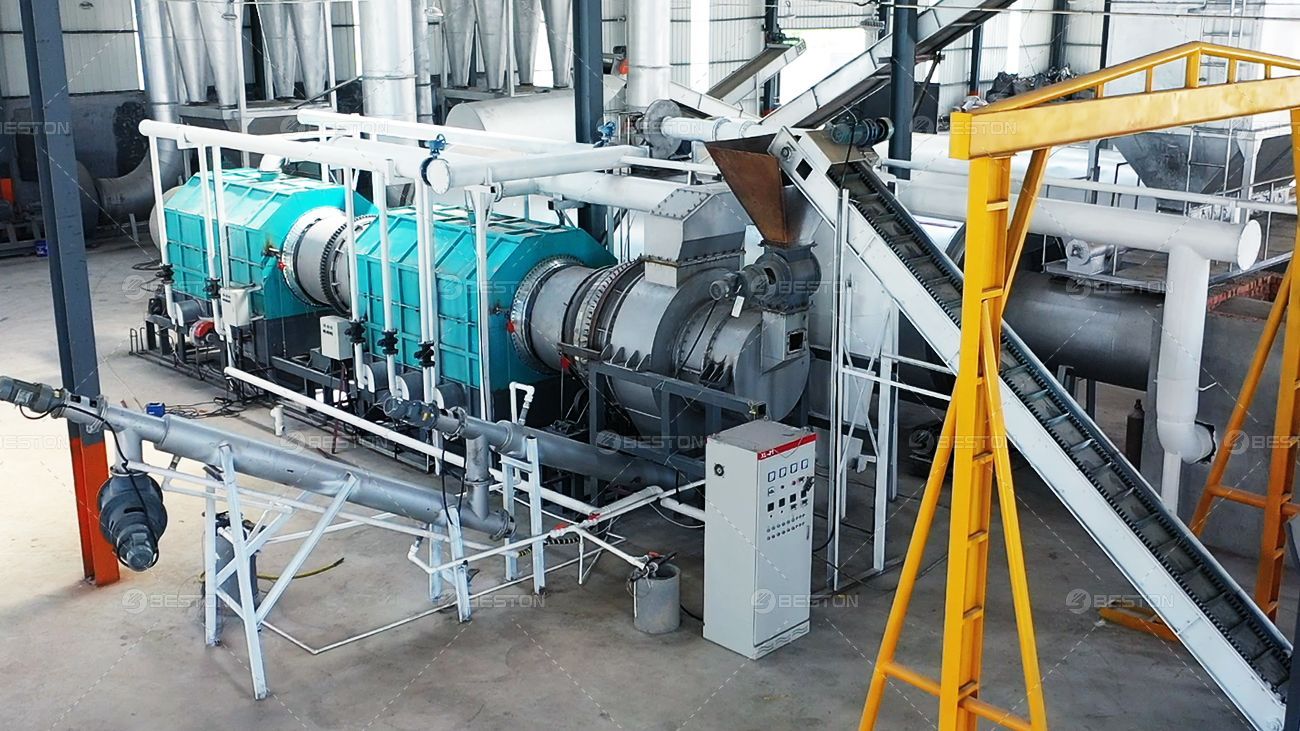
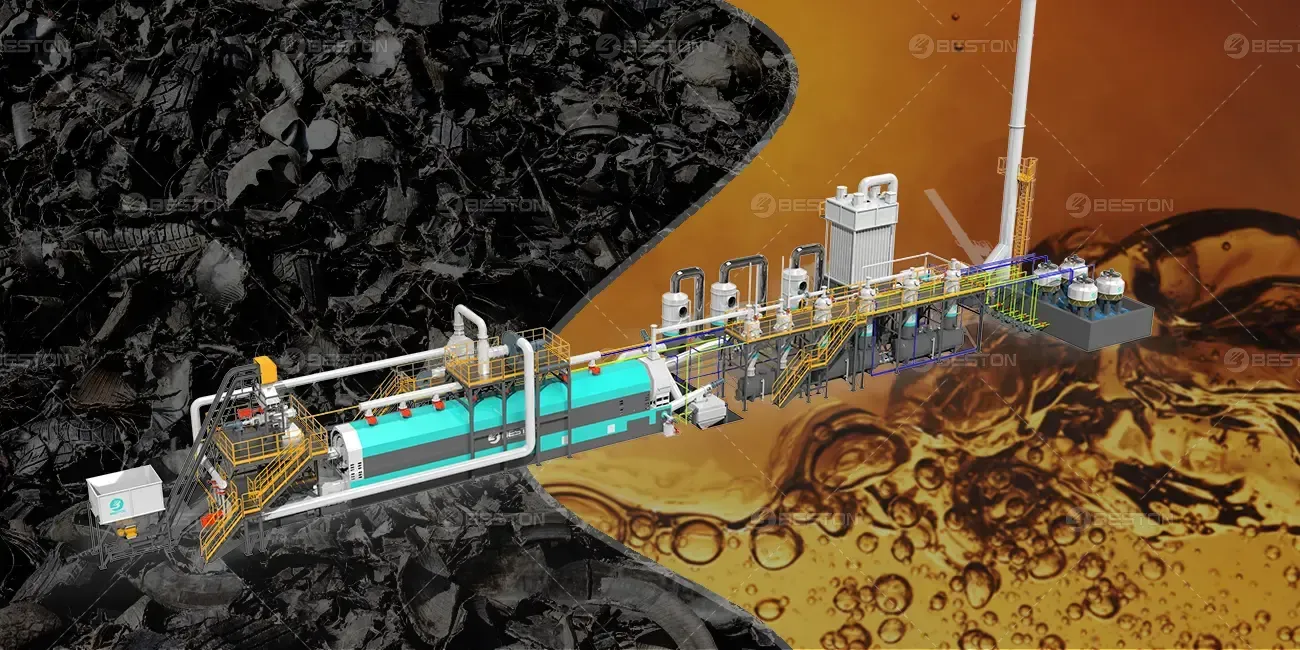