Key Information About the Biochar Production Equipment
The wood charcoal making machine, also known as a biomass carbonization machine, is used to convert various organic materials such as wood chips, tree barks, bamboo chips, tree branches, and agricultural waste into biomass charcoal through the process of carbonization.
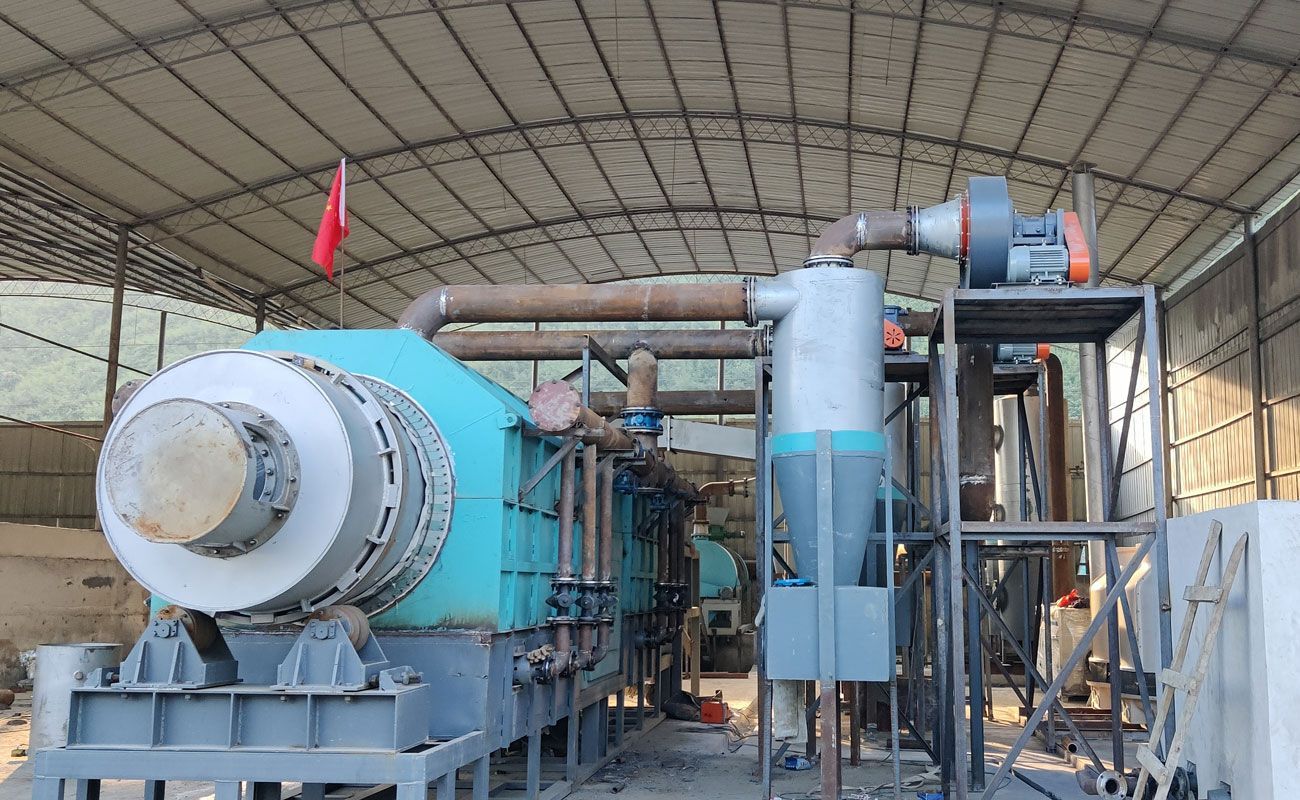
The wood charcoal making machine, also known as a biomass carbonization machine, is used to convert various organic materials such as wood chips, tree barks, bamboo chips, tree branches, and agricultural waste into biomass charcoal through the process of carbonization. This involves heating the organic matter in the absence of oxygen to produce high-quality and eco-friendly charcoal with multiple applications.
Investing in a biochar plant offers the opportunity for significant profits by selling the resulting products. Charcoal has a high demand, and the raw materials are readily available. It presents a promising business opportunity to transform waste into a valuable product. Additionally, the machine also produces by-products like biogas, tar, and wood vinegar, which add further value for the investor.
The Wood Charcoal Making Process
The wood charcoal production process comprises several steps: crushing and drying, carbonization and discharge, production of combustible gas, and recycling of gas.
However, there are important requirements for the raw materials:
The wood waste should have a moisture content below 15%. If it exceeds this level, a drying system must be implemented.
The materials should not exceed a size of 20 mm. If they are larger, a crusher needs to be used.
Here's an overview of the wood charcoal making process:
Crushing and Drying: The wood materials are crushed and dried to achieve the desired moisture content (below 15%) and size (not exceeding 20 mm). This is done using a drying system.
Carbonization and Discharge: The pre-heated wood materials are fed into the carbonization furnace. After approximately 20 minutes, the charcoal is discharged.
Production of Combustible Gas: The creation of combustible gas begins after 10 minutes of feeding the wood materials. The gas is cleaned in a cyclone dust removal system and spray dust collector, followed by separation of wood vinegar and tar in a condenser. The remaining gas is expelled from the carbonization furnace through an induced draft fan.
Recycling the Combustible Gas: The emitted combustible gas can be redirected and used to heat the carbonization reactor.
Environmental Benefits: The wood charcoal making machine promotes sustainable practices by converting organic waste into valuable charcoal. This helps reduce landfill waste and contributes to environmental preservation.
Versatile Applications: The resulting biomass charcoal generated by the machine can be used for various purposes. It is commonly used as fuel for cooking, heating, and industrial processes. Additionally, it has applications in agriculture as soil amendment and in activated carbon production.
Cost-Effective Solution: By utilizing wood waste and other organic materials, the wood charcoal making machine provides a cost-effective solution for charcoal production. It allows you to monetize waste materials while reducing expenses on disposal and purchasing traditional charcoal.
Reliable and Efficient Operation: These machines are designed for continuous operation, ensuring high productivity and efficiency. They are equipped with advanced features such as automatic feeding and discharging systems, temperature control mechanisms, and smokeless operation for improved performance.
Customizable Options: Wood charcoal making machines come in different sizes and capacities to accommodate varying production requirements. You can choose a machine that aligns with your specific needs, whether you have a small-scale operation or a large industrial facility.
Easy Maintenance: While regular maintenance is crucial for optimal performance, wood charcoal making machines are generally easy to maintain. Routine cleaning, inspection, and lubrication of the equipment components ensure longevity and consistent output.
Market Demand: There is a growing market demand for eco-friendly and sustainable products like biomass charcoal. With the right marketing strategy, you can tap into this demand and establish a profitable business.
When considering the wood charcoal making machine, it's essential to research reputable manufacturers or suppliers who offer reliable equipment, technical support, and after-sales service. Additionally, familiarize yourself with local regulations and policies concerning the production and sale of biomass charcoal.
The wood charcoal making machine presents a valuable opportunity to transform waste materials into a profitable product while contributing to environmental sustainability. With careful planning, investment, and efficient operation, you can establish a successful business venture in the biochar industry.
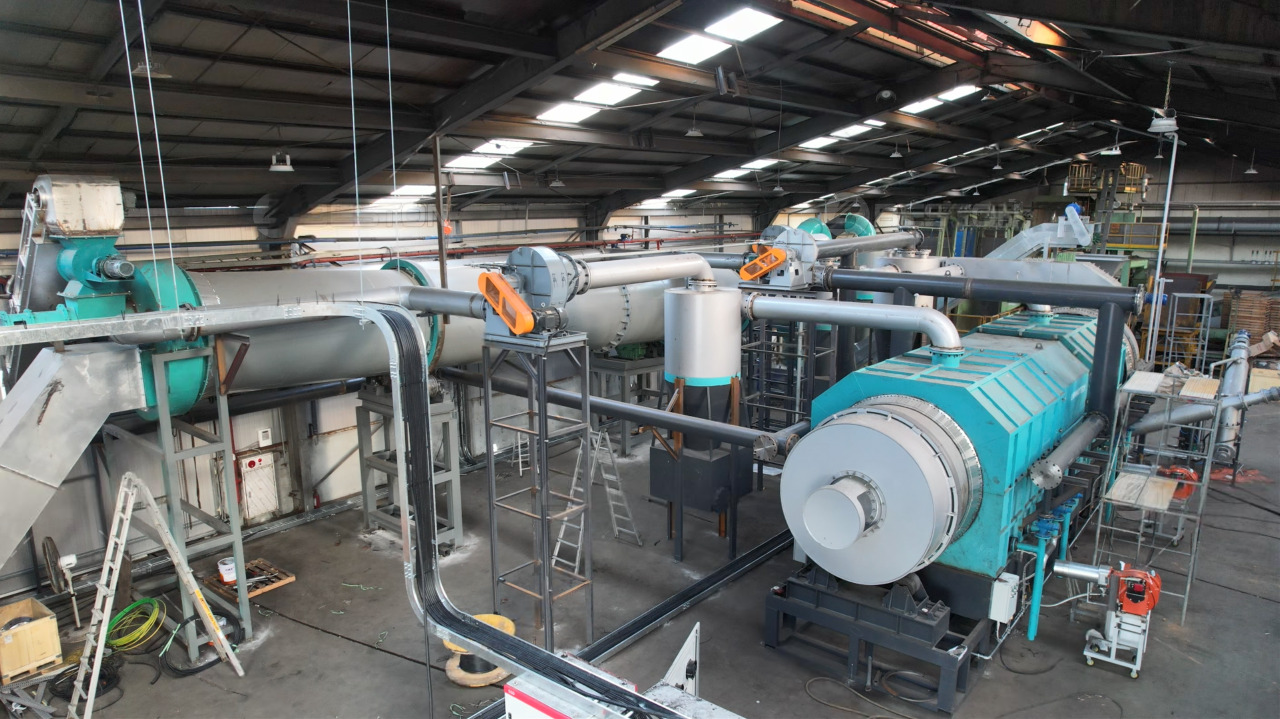
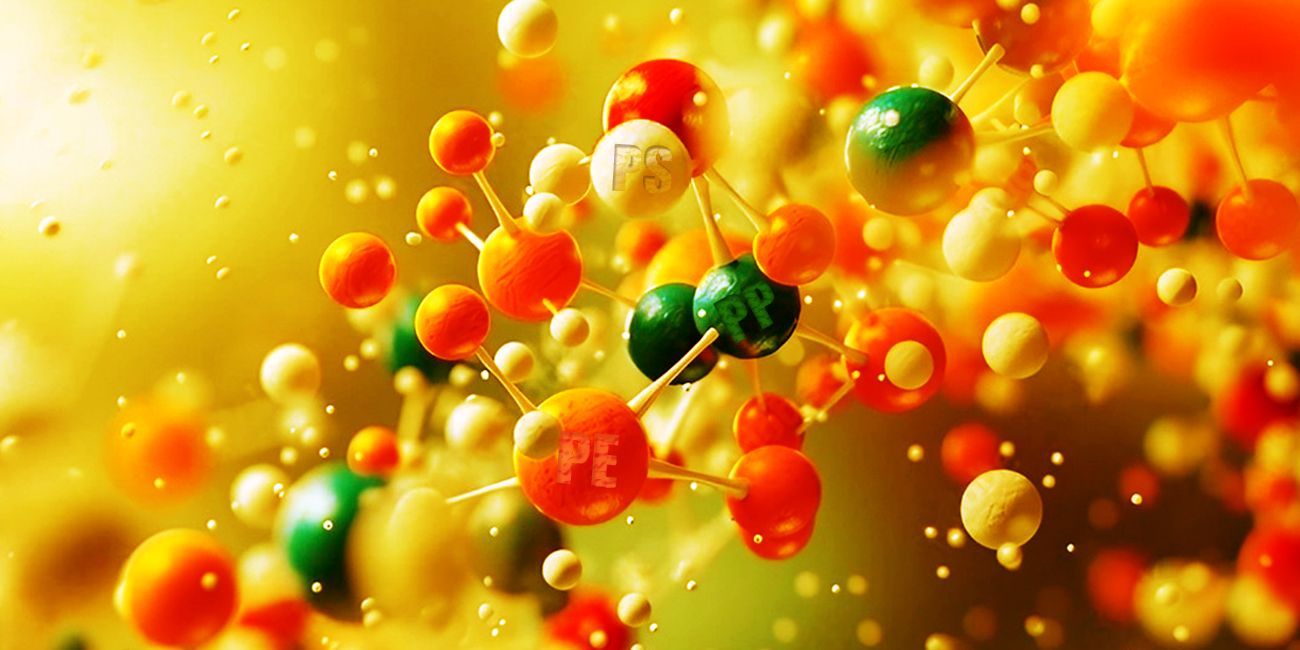