Detailed Component Analysis of Plastic Pyrolysis Oil
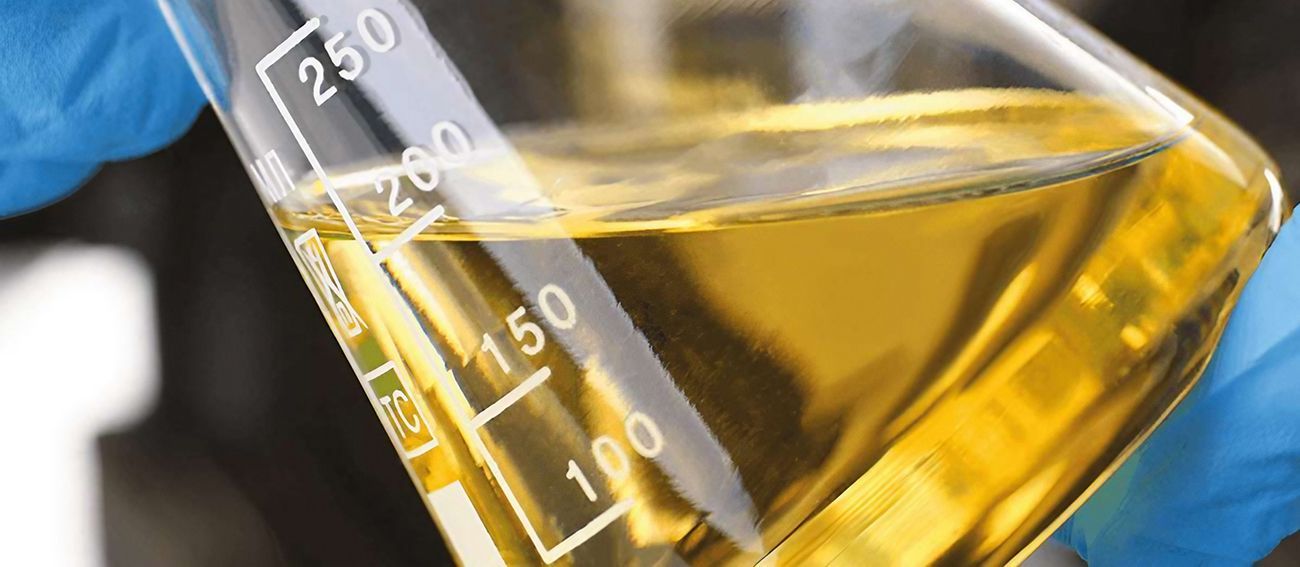
The process of converting plastic waste into valuable products such as pyrolysis oil has gained considerable attention due to its potential to reduce environmental pollution while generating useful byproducts. Pyrolysis oil, one of the primary outputs of a plastic pyrolysis plant, plays a crucial role in the energy sector. However, the quality and characteristics of the oil produced can vary significantly depending on factors such as feedstock composition, operating conditions, and scale of the plant. This article delves into the detailed component analysis of plastic pyrolysis oil, shedding light on its key constituents, variations, and implications for commercial use.
1. Composition of Plastic Pyrolysis Oil
Plastic pyrolysis oil is a complex mixture of hydrocarbons, primarily consisting of aliphatic and aromatic compounds. The specific chemical composition of the oil depends on the type of plastic for pyrolysis machinery, the temperature, and the duration of pyrolysis. Typical components of pyrolysis oil include:
- Alkanes (paraffins): These are saturated hydrocarbons found in the oil, usually contributing to its calorific value. Alkanes can vary in chain length, and their presence is influenced by the feedstock and process conditions.
- Aromatics: Benzene, toluene, and xylene are common aromatic compounds found in pyrolysis oil. These chemicals are valuable as solvents and are used in various industrial applications. The concentration of aromatics increases when processing plastics such as polystyrene and PET.
- Olefins (alkenes): Unsaturated hydrocarbons are also present in plastic pyrolysis oil. Olefins can undergo further reactions and are often precursors to the production of more refined chemical products.
- Oxygenated compounds: Oxygenated molecules such as aldehydes, ketones, and acids are commonly found in pyrolysis oil. These compounds contribute to the oil’s corrosive nature and can affect its suitability for fuel production without proper refinement.
The chemical composition of the pyrolysis oil determines its potential applications, such as in the production of synthetic fuels, chemicals, and as a raw material for further refinement.
2. Variations Based on Feedstock and Scale
The feedstock used in a plastic pyrolysis plant plays a significant role in determining the quality and characteristics of the oil produced. For instance, plastics like polyethylene (PE) and polypropylene (PP) typically yield oils with higher aliphatic hydrocarbon content, making them more suitable for use as fuels. On the other hand, plastics such as polystyrene (PS) and polyethylene terephthalate (PET) produce oils with a higher concentration of aromatic compounds, which are more valuable in the chemical industry.
The scale of the pyrolysis plant—whether small scale or large scale—also influences the composition of the oil. Small scale pyrolysis plants tend to operate at lower temperatures and can produce oil with varying qualities depending on the consistency of feedstock and temperature control. Large scale pyrolysis plants, with more advanced control systems, can offer more consistent outputs with higher yields of pyrolysis oil, especially when advanced technologies such as continuous reactors are employed.
In larger plants, the optimization of process parameters such as temperature, pressure, and residence time can be precisely managed, leading to a more refined and uniform product. This consistency is crucial for ensuring the commercial viability of the oil produced.
3. Influence of Temperature on Oil Composition
The temperature at which the pyrolysis process is carried out significantly affects the composition of the resulting oil. Typically, the pyrolysis of plastic waste occurs within the temperature range of 350°C to 600°C. The temperature influences the cracking of polymer chains and the production of different types of hydrocarbons.
Low temperatures (350°C - 450°C): At these temperatures, the oil produced tends to have a higher content of heavier hydrocarbons, including waxes and oils with high molecular weight. These oils are less volatile and require further refining to be used as fuel.
High temperatures (500°C - 600°C): Higher pyrolysis temperatures promote the production of lighter, more volatile compounds, which are often more suitable for fuel applications. The increased temperature also encourages the formation of smaller, low molecular weight molecules, including alkanes and aromatics.
Thus, the temperature plays a crucial role in determining whether the pyrolysis oil is suited for energy generation or for chemical applications, with higher temperatures typically leading to a more fuel-efficient product.
4. Refining and Upgrading Plastic Pyrolysis Oil
Raw plastic pyrolysis oil, while useful, often contains impurities such as sulfur, nitrogen, and oxygenated compounds that reduce its market value, especially in the fuel industry. To make the oil more commercially viable, further treatment or upgrading is necessary. Some common refining techniques include:
Hydroprocessing: This method involves treating the oil with hydrogen to remove sulfur and nitrogen compounds, as well as to saturate the aromatic compounds, transforming them into aliphatic compounds. This is particularly important for improving the oil’s performance as a diesel substitute.
Distillation: Fractional distillation can be used to separate different hydrocarbon fractions within the oil. This helps in isolating valuable products such as light oils and gases, which can be used as fuels or in petrochemical production.
Blending: Plastic pyrolysis oil can also be blended with other types of fuel to enhance its properties and improve its efficiency in engines and industrial burners.
The need for refining underscores the complexity of plastic pyrolysis oil as a feedstock. While it holds significant promise, the oil requires attention to detail and further processing to meet specific industry standards.
5. Potential Applications of Pyrolysis Oil
The versatility of plastic pyrolysis oil makes it an attractive feedstock for various applications. These include:
Fuel production: When appropriately refined, pyrolysis oil can be used as a substitute for conventional diesel or gasoline in internal combustion engines, generators, and industrial boilers.
Chemical feedstock: Pyrolysis oil contains valuable chemicals, such as toluene and xylene, which can be extracted and used as raw materials in the production of plastics, solvents, and other chemicals.
Energy generation: In some cases, the oil can be converted into syngas for use in electricity generation, offering an additional revenue stream for pyrolysis plants.
6. Challenges and Future Outlook
While the potential of plastic pyrolysis oil is undeniable, challenges remain in its commercial viability. Variability in oil composition due to differences in feedstock types and operational conditions can complicate large-scale production. Continued advancements in pyrolysis technology, coupled with improvements in refining processes, will help maximize the value of the oil produced.
In conclusion, understanding the component analysis of plastic pyrolysis oil is essential for assessing its economic potential. By optimizing feedstock selection, operational conditions, and refining techniques, pyrolysis plants can unlock the full value of this versatile product. Whether operating on a small scale or large scale, addressing these factors will determine the overall success of the process.
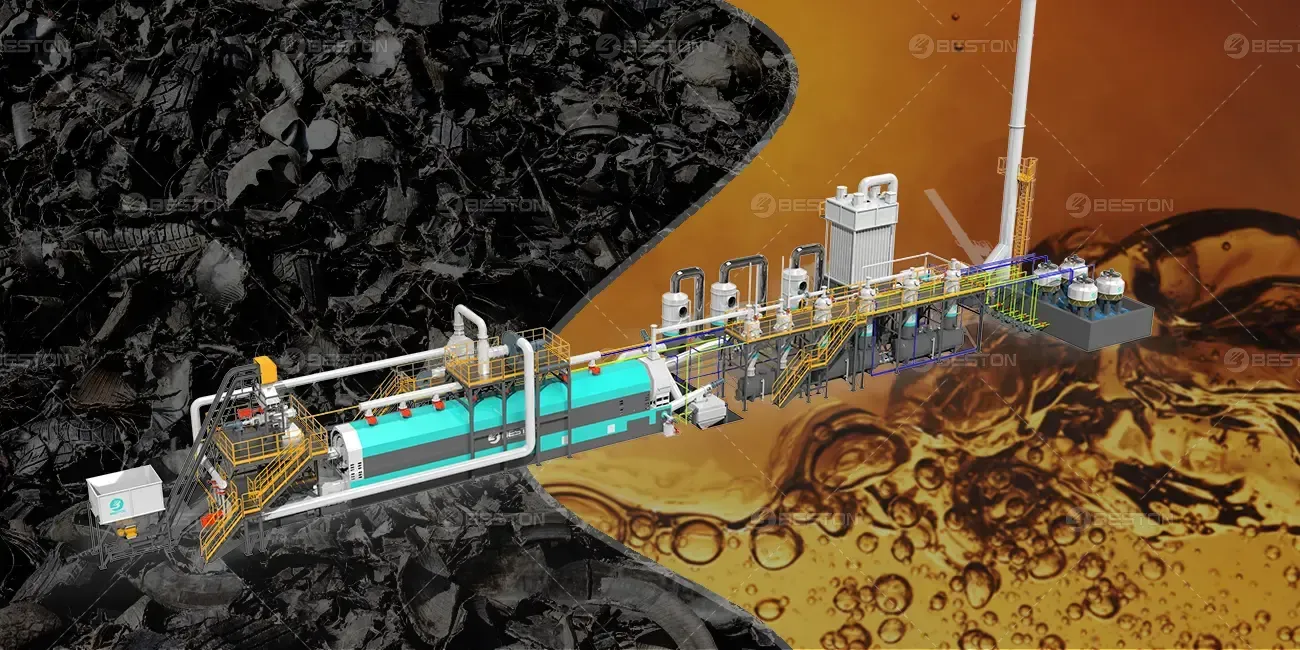
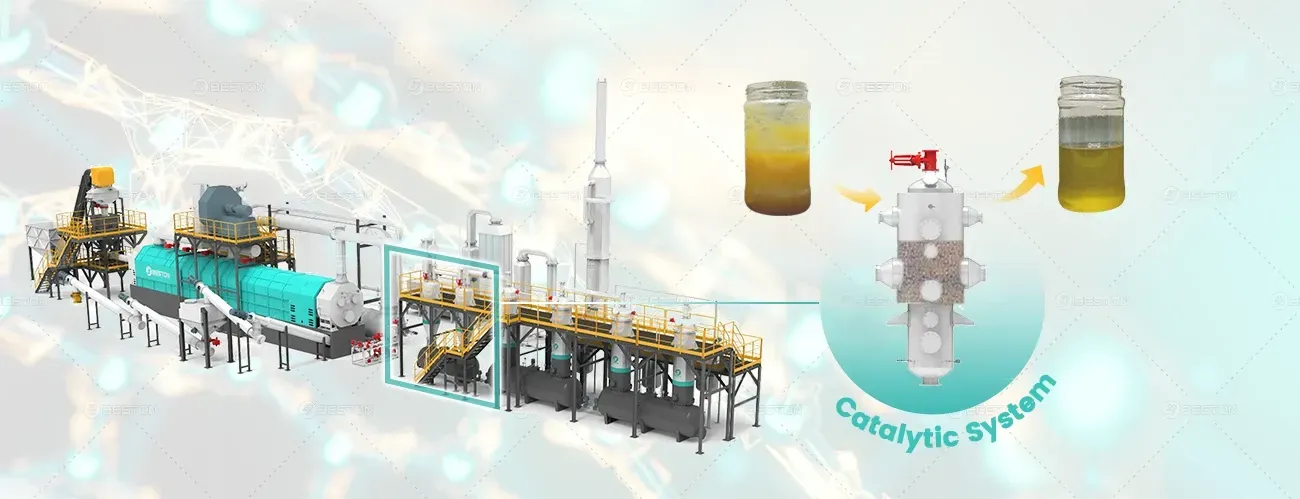